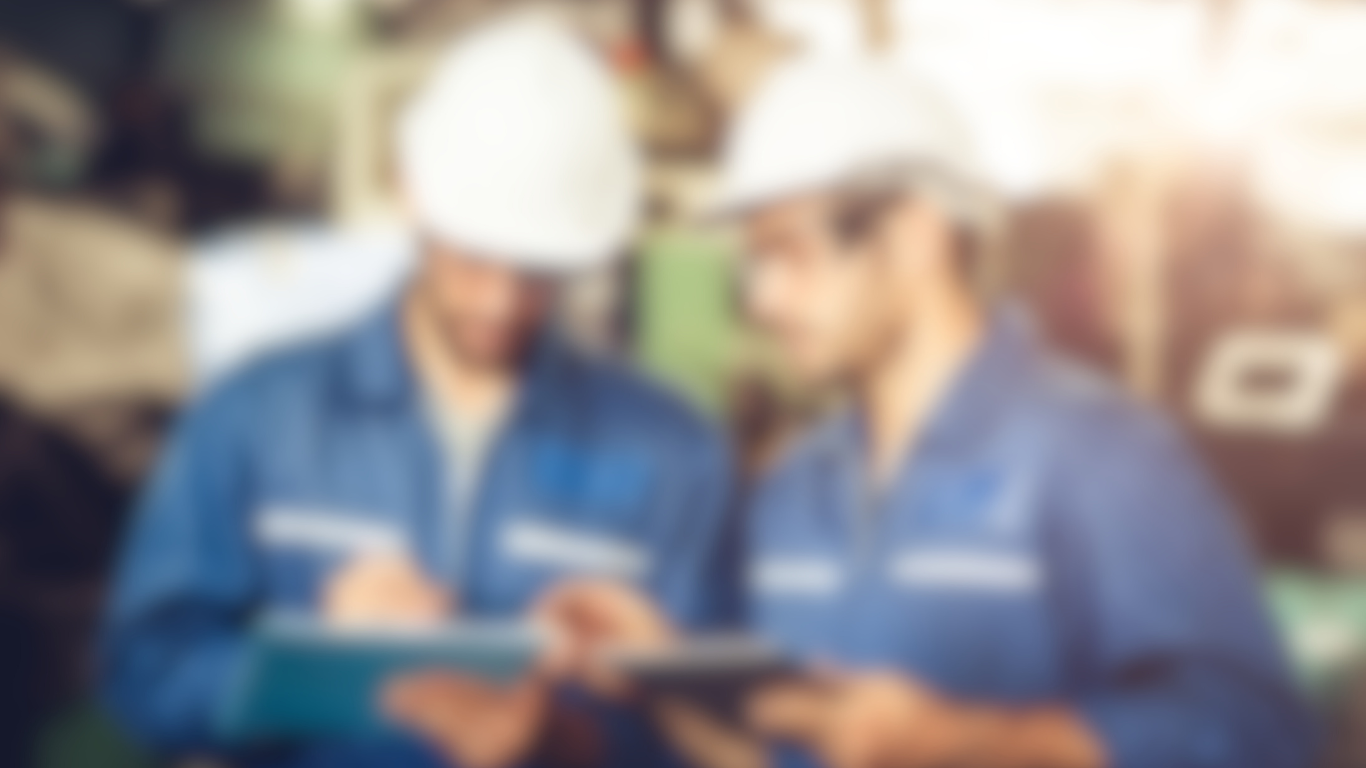
Operator Asset Care (OAC)
Empowering frontline employees to take ownership of equipment maintenance is a cornerstone of modern asset management strategies. Operator Asset Care (OAC) is a structured approach that involves operators in the upkeep of their machinery, leading to enhanced equipment reliability, reduced downtime, and a proactive maintenance culture.
At MCP Consulting Group, we offer tailored consultancy services to assist organisations in implementing and sustaining effective OAC programmes.
TPM, AM and OAC SUB-CATEGORIES
What is
Operator Asset Care
Operator Asset Care (OAC) is a methodology that integrates equipment operators into the maintenance process, enabling them to perform routine tasks such as cleaning, lubrication, and basic inspections. This approach not only enhances the operators' understanding of their equipment but also facilitates early detection of potential issues, thereby preventing unexpected failures and promoting a collaborative maintenance environment.
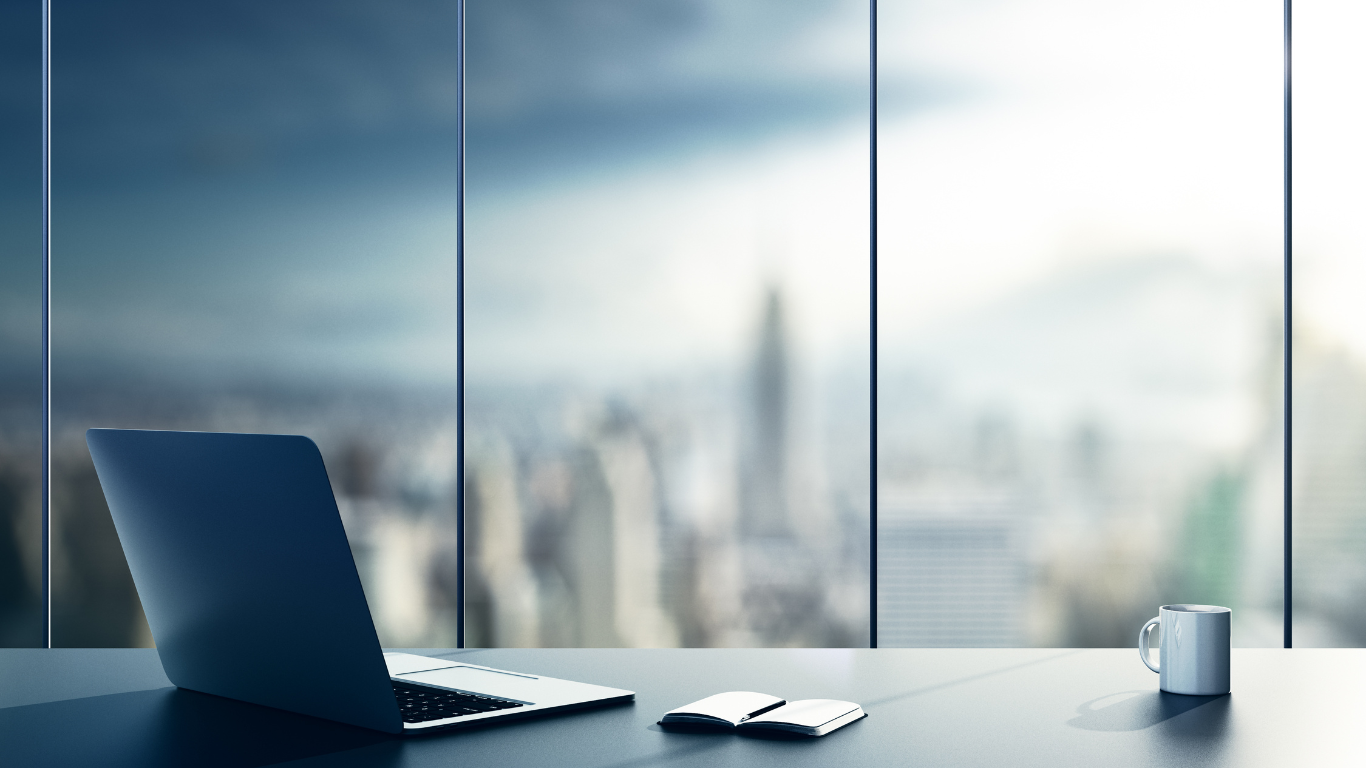
Key Objectives of
Operator Asset Care
By involving operators in regular maintenance activities, organisations can identify and address minor issues before they escalate, leading to improved equipment uptime.
1
Enhancing Equipment Reliability
Reducing Maintenance Costs
2
Early detection and resolution of equipment anomalies minimise the need for extensive repairs, thereby lowering maintenance expenses.
Empowering Operators
3
Providing operators with the skills and responsibility for basic maintenance tasks fosters a sense of ownership and accountability, contributing to a more engaged workforce.
Driving Continuous Improvement
OAC bridges the gap between operations and maintenance teams, promoting better communication and teamwork.
4
Fostering a Collaborative Maintenance Culture
5
Through regular monitoring and feedback, OAC encourages ongoing enhancements in maintenance practices and equipment performance.
The
7 Stages of OAC
Basic Cleaning by Operators - Operators engage in routine cleaning to become familiar with their equipment and identify abnormalities.
1
2
Eliminating Causes of Pollution and Contamination – Identifying and mitigating sources of contamination that can affect equipment performance.
Standard for Basic Maintenance - Establishing clear procedures for routine maintenance tasks performed by operators.
3
4
Developing Operators’ Skills - Enhancing operators' technical knowledge and problem-solving abilities.
Standards for Independent Inspection - Empowering operators to conduct independent equipment inspections.
5
Organisation and Visual Management - Implementing visual tools to monitor equipment status and maintenance activities.
6
Continuous Improvement - Encouraging ongoing evaluation and enhancement of maintenance practices.
7
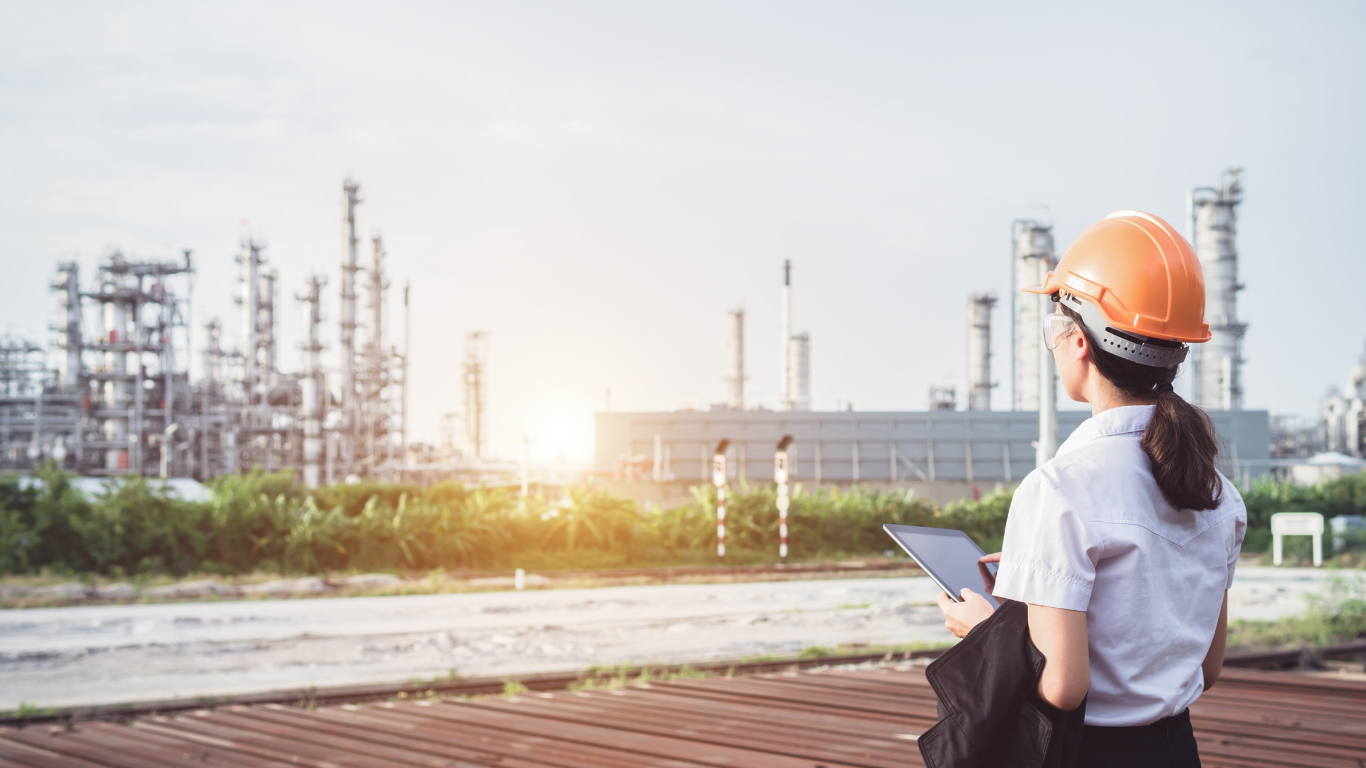
MCP Approach to
Operator Asset Care
Assessment of Current Practices
We begin by evaluating existing maintenance procedures and operator involvement to identify areas for improvement.
Customised OAC Framework Development
Our team collaborates with your organisation to design a tailored OAC programme that aligns with your operational goals and workforce capabilities.
Training and Skill Development
We provide comprehensive training to equip operators with the necessary skills for effective equipment care.
Implementation Support
Our consultants assist in rolling out the OAC programme, ensuring seamless integration into daily operations.
Continuous Monitoring and Improvement
We establish mechanisms for ongoing assessment and refinement of the OAC programme to ensure its long-term success.
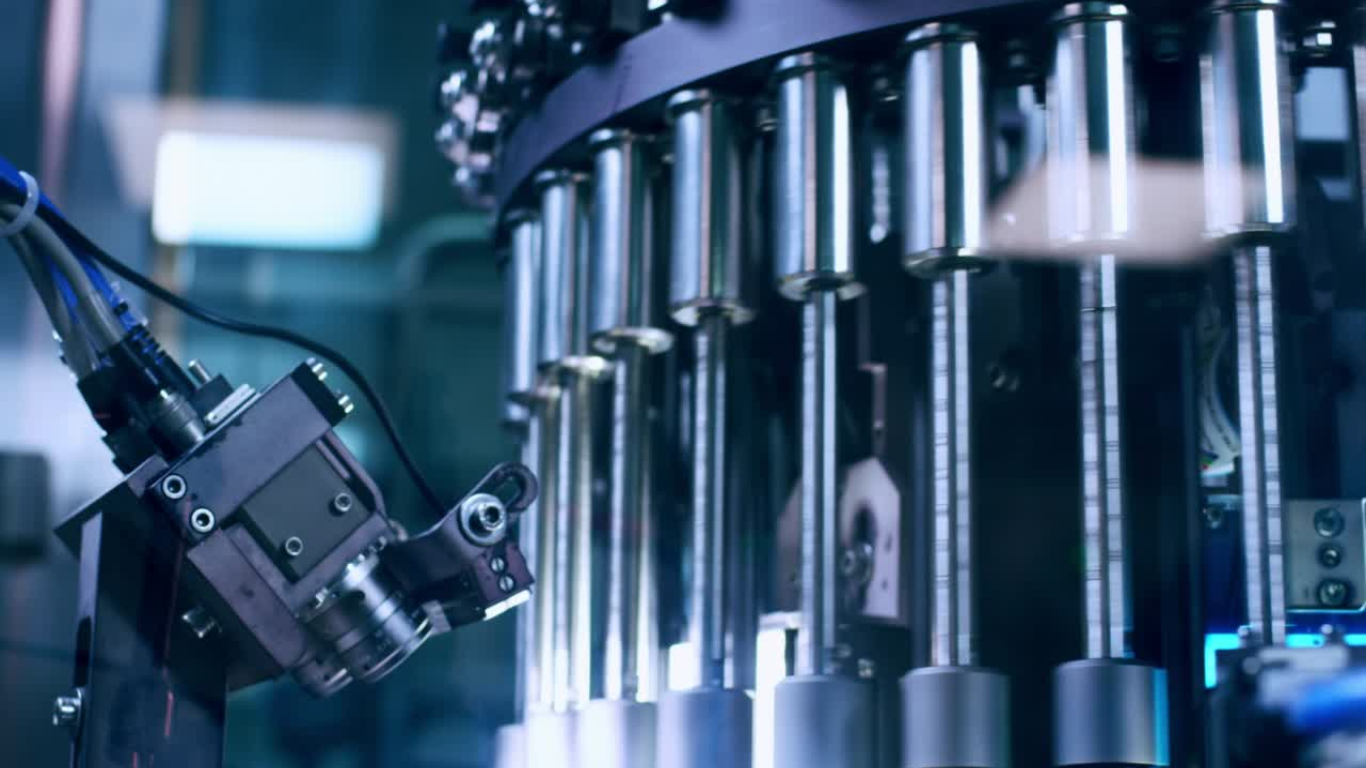
TPM, AM and OAC
Explore More
Speak to One of Our
Experienced Consultants
If you have any questions or would like to learn more about how MCP can support your organisation with Autonomous Maintenance, please get in If you have any questions or would like to learn more about how MCP Consulting Group can support your organisation with Operator Asset Care, please get in touch with us.
Our team of consultants is ready to provide tailored solutions to optimise maintenance strategies, empower your workforce, and enhance equipment reliability. Contact us today to discuss your specific requirements.
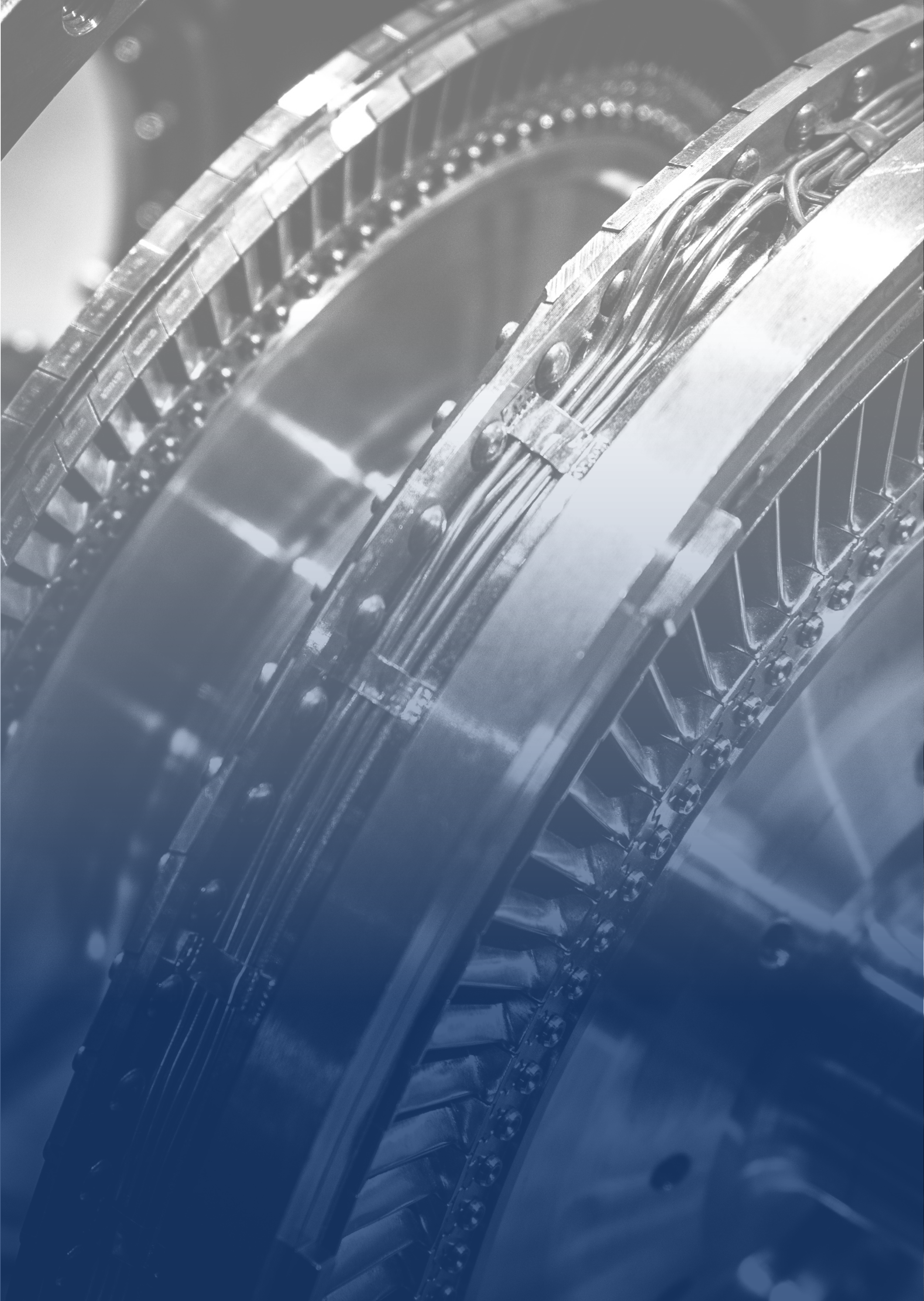
FAQs
-
While both involve operators in maintenance tasks, OAC is a broader concept that encompasses various maintenance activities, whereas Autonomous Maintenance is a specific pillar of Total Productive Maintenance focusing on operator-performed maintenance.
-
OAC is applicable across various sectors, including manufacturing, food processing, pharmaceuticals, and energy, where equipment reliability is crucial.
-
By enabling early detection of equipment issues and reducing the frequency of major repairs, OAC helps lower maintenance costs.
-
Operators receive training in basic maintenance tasks, equipment operation, and problem-solving techniques to effectively participate in the OAC programme.
-
Involving operators in maintenance tasks fosters a sense of ownership and responsibility, leading to increased job satisfaction and engagement.