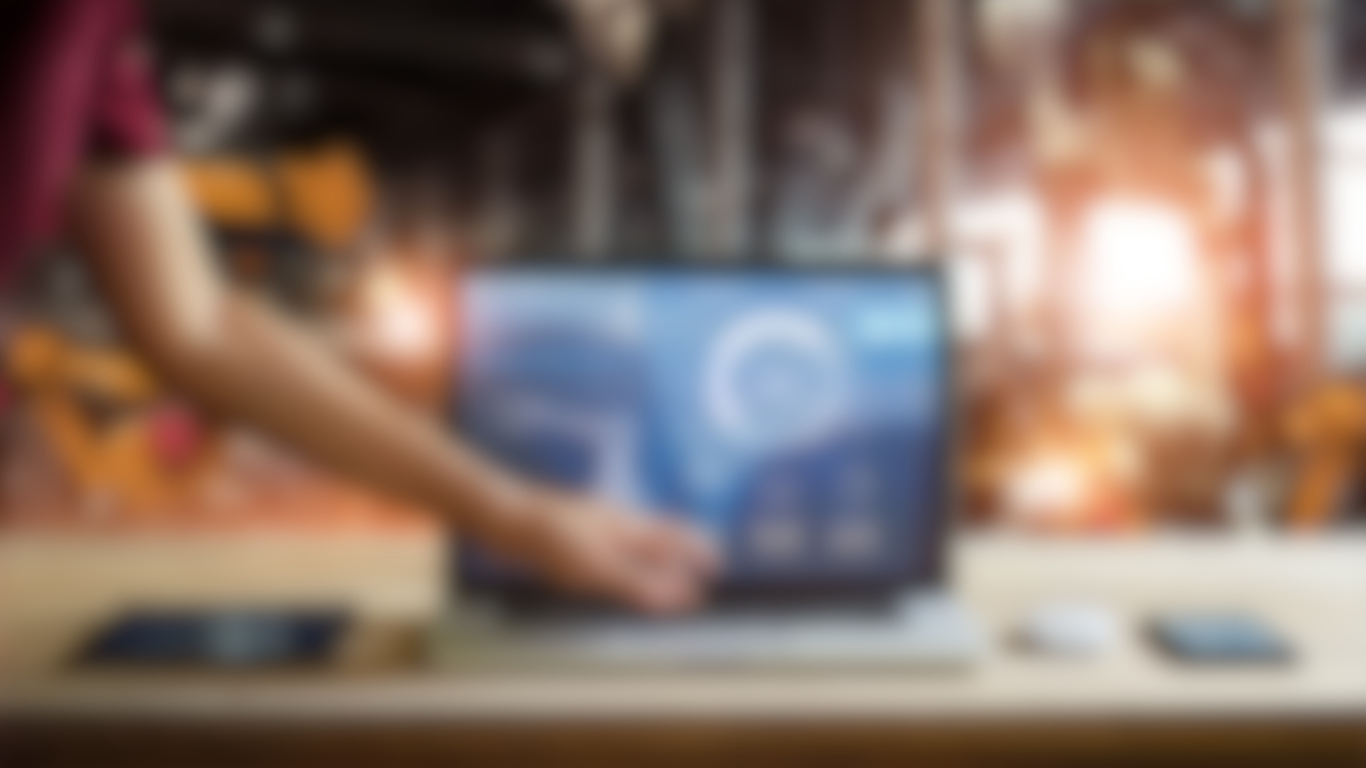
Operational Excellence
Achieving Operational Excellence means aligning processes, maintenance strategies, and performance management across the organisation. Our structured programme helps identify inefficiencies, standardise best practices, and embed sustainable improvements across multiple sites.
At MCP Consulting Group, we support businesses in implementing tailored frameworks that enhance performance, improve consistency, and deliver measurable results.
Download Our eBook - First Steps to Operational Excellence
What is
Operational Excellence
Operational Excellence (OE) is a strategic approach focused on improving business performance by aligning processes, people, and systems across all sites and departments. It enables organisations to enhance productivity, reduce waste, and deliver consistent results.
In multi-site environments, OE becomes essential for standardising practices, enabling meaningful performance comparisons, and supporting the effective use of systems such as SAP, Maximo, or CMMS platforms. MCP’s Operational Excellence programmes ensure a unified and structured approach to improvement across the organisation.
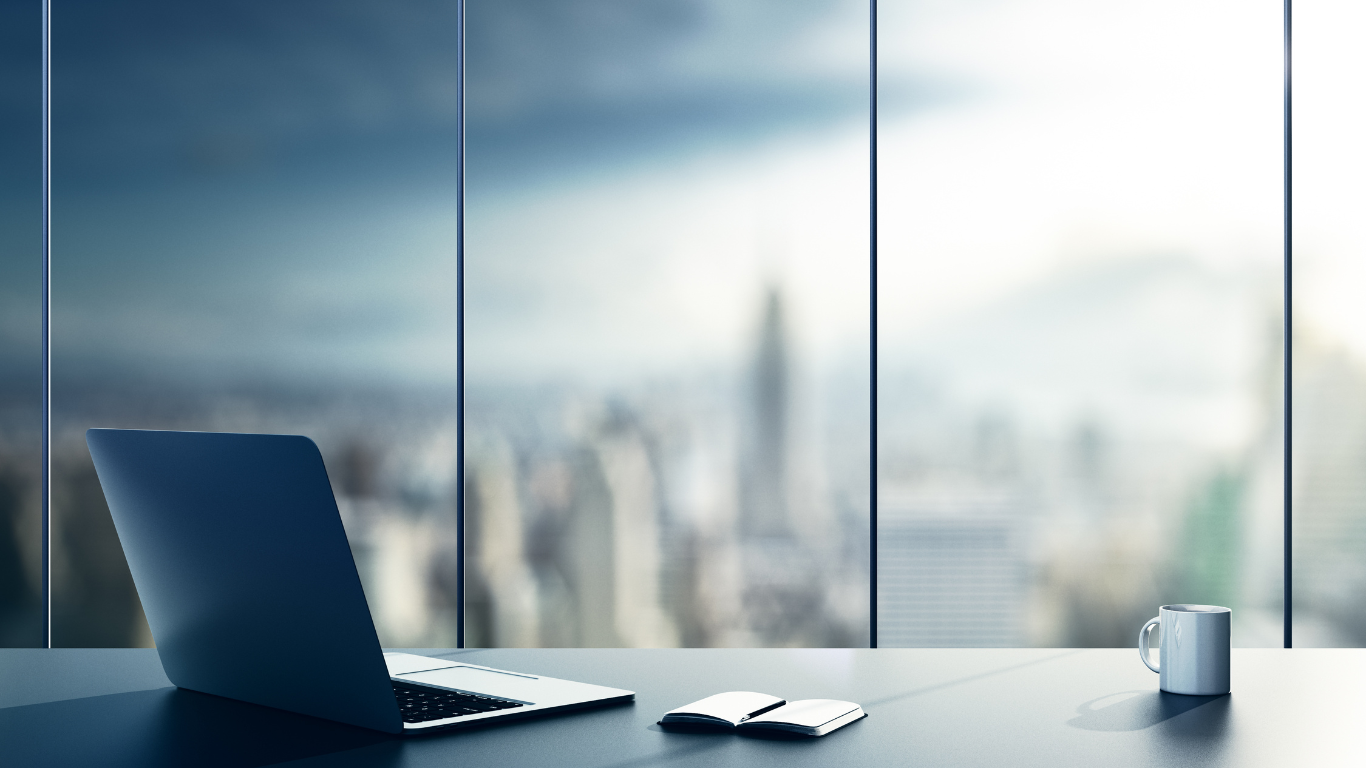
Key Pillars of
Operational Excellence
At MCP, we focus on four key performance areas that underpin an effective Operational Excellence programme:
Maintenance Management
Production Management
Reliability Management
Performance Management
These pillars work together to create a foundation for continuous improvement and operational resilience.

The Foundations of
Operational Excellence
While many organisations have successfully standardised areas such as HR, finance, and production, maintenance and asset management are often left to evolve independently across sites. This inconsistency can hinder the effectiveness of enterprise-wide systems such as SAP, Maximo, or CMMS platforms, making it difficult to compare performance and drive improvement across the business.
A CONSITENT APPROACH
A consistent approach to maintenance and asset management enables:
Alignment with corporate systems and strategic goals
Improved equipment reliability, performance, and uptime
More effective use of planning tools and operational resources
Standardised processes for clearer performance benchmarking
Greater compliance, risk control, and operational confidence
Equipment reliability and availability
Work planning and scheduling
Spare parts and inventory control
Standardisation of business processes
Organisation structure and role clarity
Document and data management
Effective use of CMMS and maintenance systems
Training and workforce skills development
THE GREATEST VALUE
High-performing organisations also ensure their improvement efforts are directed at the areas that deliver the greatest value to the business. These include:
By focusing on both consistency and strategic priorities, organisations lay the groundwork for sustainable, measurable improvement across their operations.
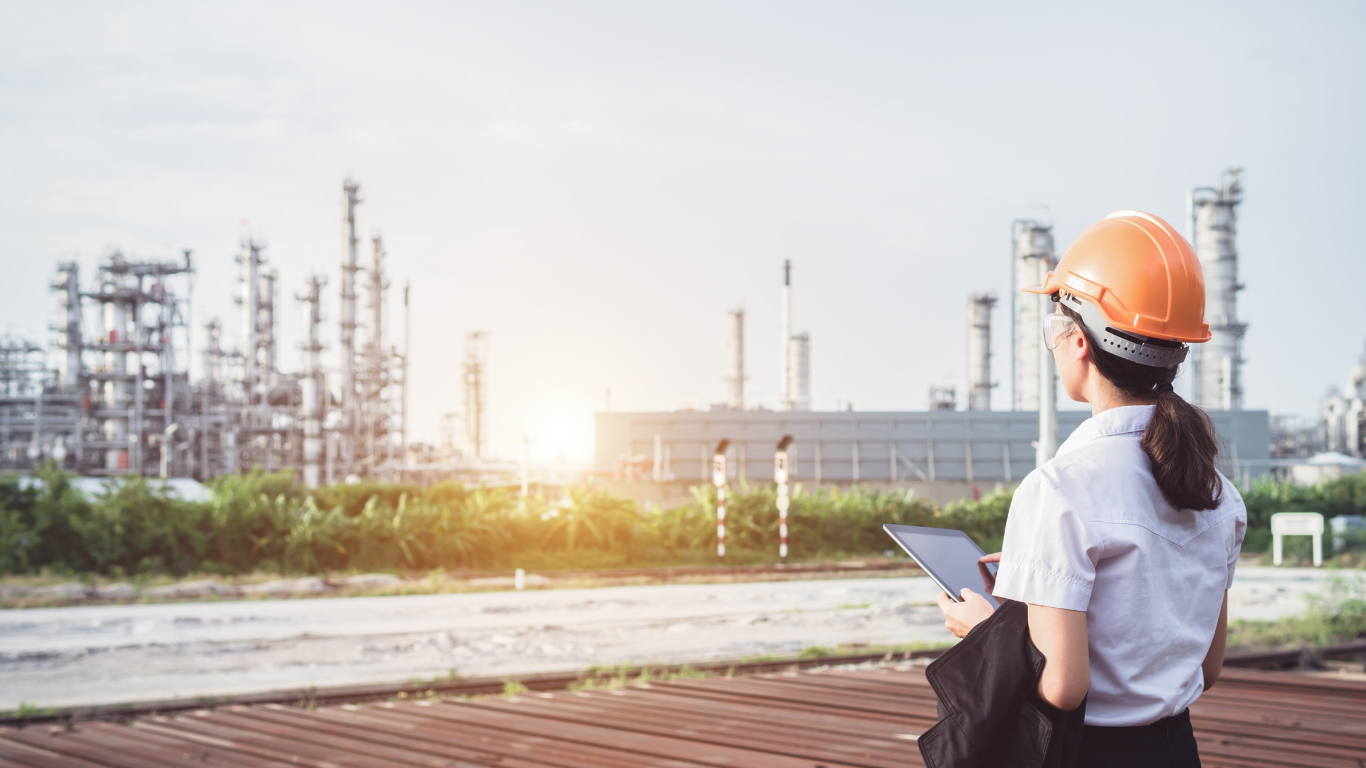
MCP Approach to
Operational Excellence
MCP has nearly 50 years of experience delivering Operational Excellence programmes across sectors such as food & drink, pharmaceuticals, medical devices, automotive, paper, airports, and facilities.
Our structured five-stage process includes:
Gap analysis using MCP’s proprietary AMIS assessment model to benchmark current practices against industry standards.
1
Initial Assessment
Implementation Planning
2
Developing a phased roadmap aligned with your business objectives, prioritising key workstreams and site-specific needs.
Implementation Programme
3
On-site delivery supported by MCP consultants and trainers, with local champions leading improvement initiatives.
Training
Measuring and reporting on outcomes to ensure improvements are embedded and value is sustained over time.
4
Benefit Realisation
5
Training is often embedded into our programmes, ensuring teams understand and apply the tools and techniques required to drive improvement.
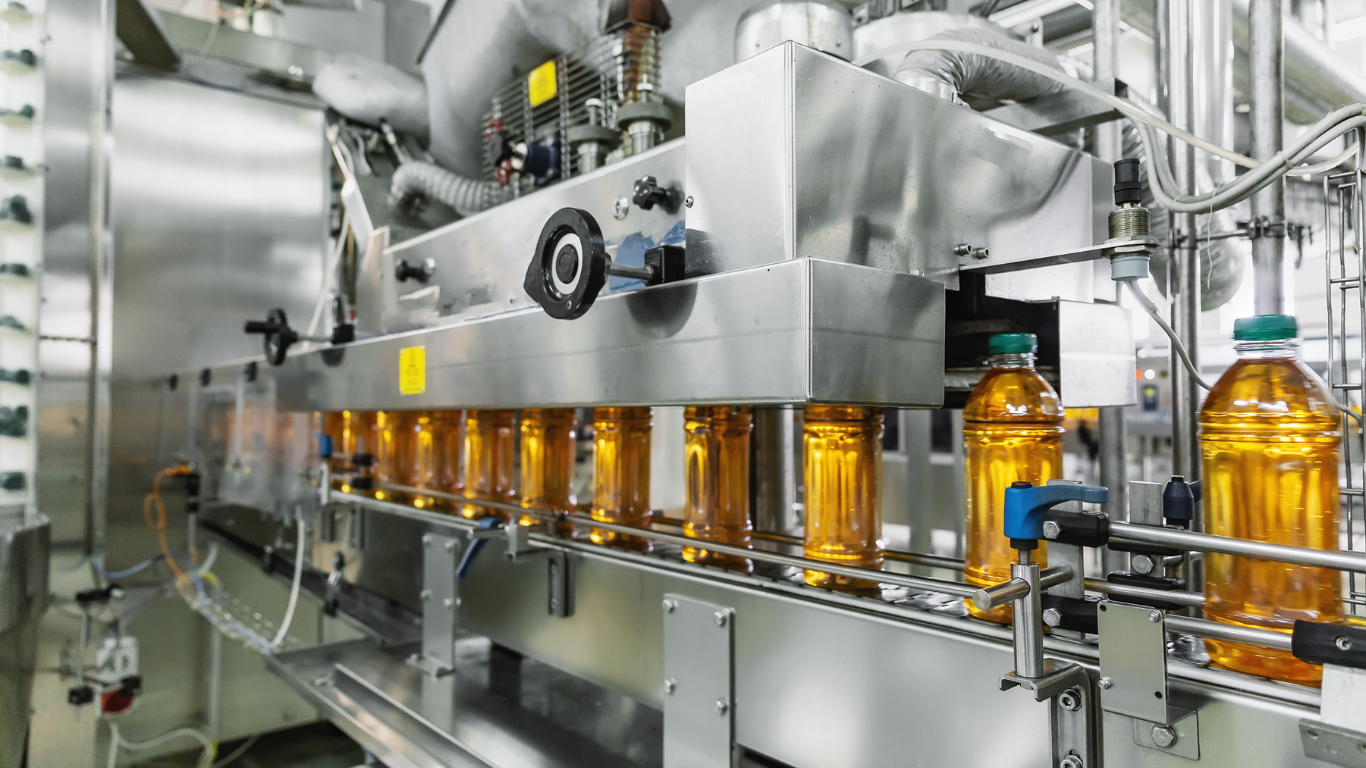
The Benefits of
Operational Excellence
Clients who have partnered with MCP have achieved:
Breakdowns reduced by up to 50%
<50%
Removal of 25–50% of unnecessary preventive maintenance hours
<50%
Productivity increases of 40–80%
<80%
Manufacturing cost reductions of up to 20%
<20%
Maintenance cost savings of up to 20%
<20%
Quality costs reduced by up to 30%
<30%
Productivity gains of up to 20%
<20%
Curious about how your maintenance practices compare to world-class standards?
Mini AMIS Assessment
Take our complimentary Mini AMIS Assessment to discover how your results stack up against other businesses in the manufacturing sector. Our experts will generate a personalised report, highlighting your strengths and areas for improvement.
Speak to One of Our
Experienced Consultants
If you are ready to take the next step in your Operational Excellence journey, or would like to explore how MCP Consulting Group can support your organisation, we’d be delighted to hear from you.
Our experienced consultants are on hand to develop tailored solutions that improve consistency, enhance performance, and deliver measurable, long-term results. Contact us today to discuss your goals and discover how we can help you achieve sustainable operational improvement.
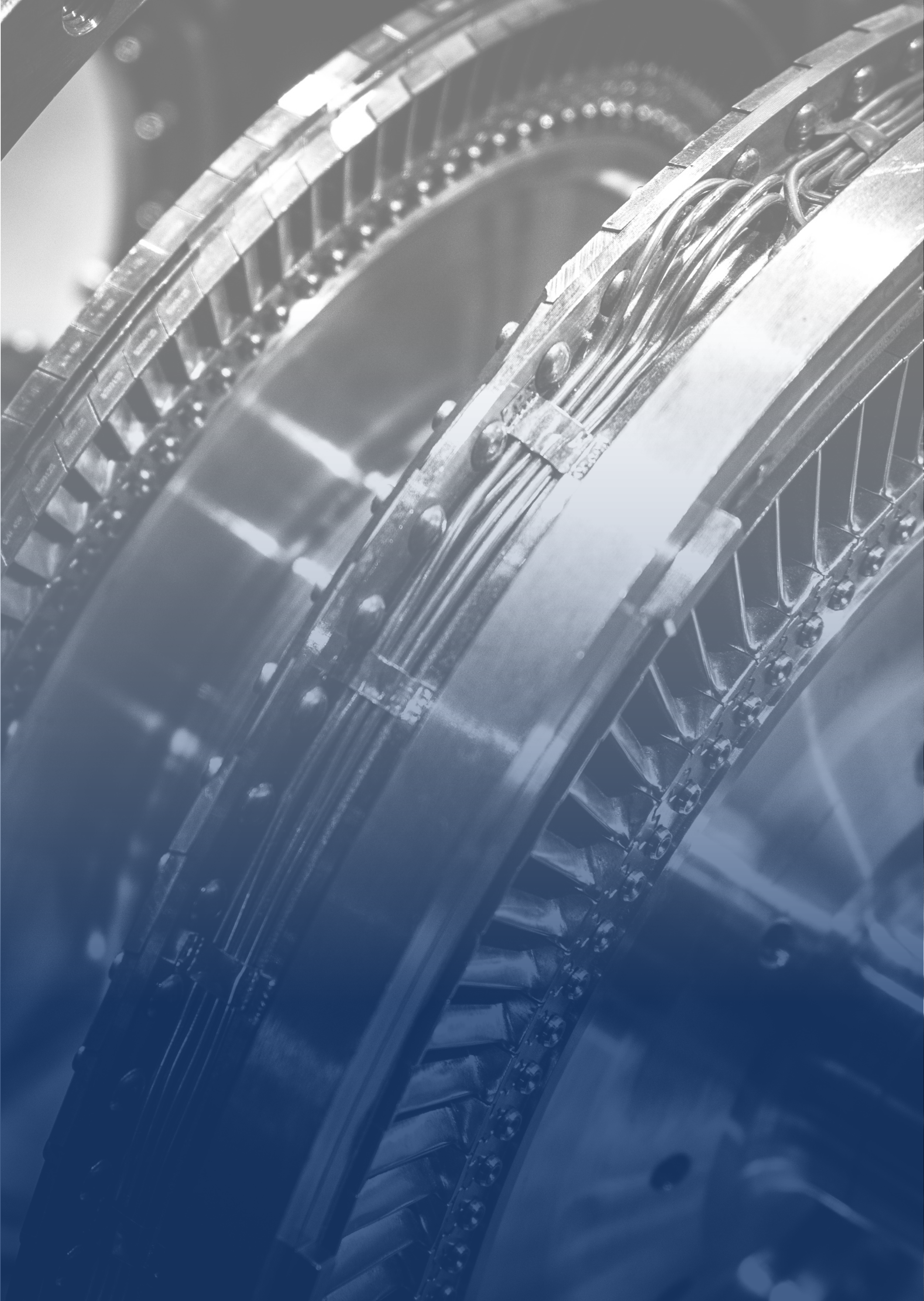
FAQs
-
Continuous Improvement focuses on incremental changes over time, often led from within departments. Operational Excellence is a broader, strategic approach that aligns people, processes, and systems across the entire organisation to deliver sustainable, measurable improvements.
-
The duration varies depending on the size and complexity of the organisation. A typical programme may span 1 to many years, beginning with assessment and planning, followed by phased implementation and benefit realisation. MCP tailors each programme to suit your specific requirements and pace of change.
-
No. While it originated in manufacturing, Operational Excellence principles are now widely applied in sectors such as pharmaceuticals, food & drink, facilities, healthcare, and transportation. Any asset-intensive or process-driven organisation can benefit from adopting an OE framework.
-
MCP works with you to define success criteria at the outset. Typical performance indicators include reduced breakdowns, lower maintenance costs, increased productivity, improved asset availability, and enhanced workforce capability. These are measured against your baseline using our AMIS assessment model and tracking tools.
-
AMIS (Asset Maintenance Improvement System) is MCP’s proprietary assessment tool used to benchmark your current practices against best-in-class standards. It forms the foundation of the Initial Assessment phase and supports ongoing measurement, planning, and improvement tracking.
-
Yes. MCP has extensive experience working with multi-site organisations, helping ensure consistent practices, aligned KPIs, and successful delivery across all locations. We provide a combination of on-site consultancy, remote support, and structured training to deliver sustainable, scalable results.