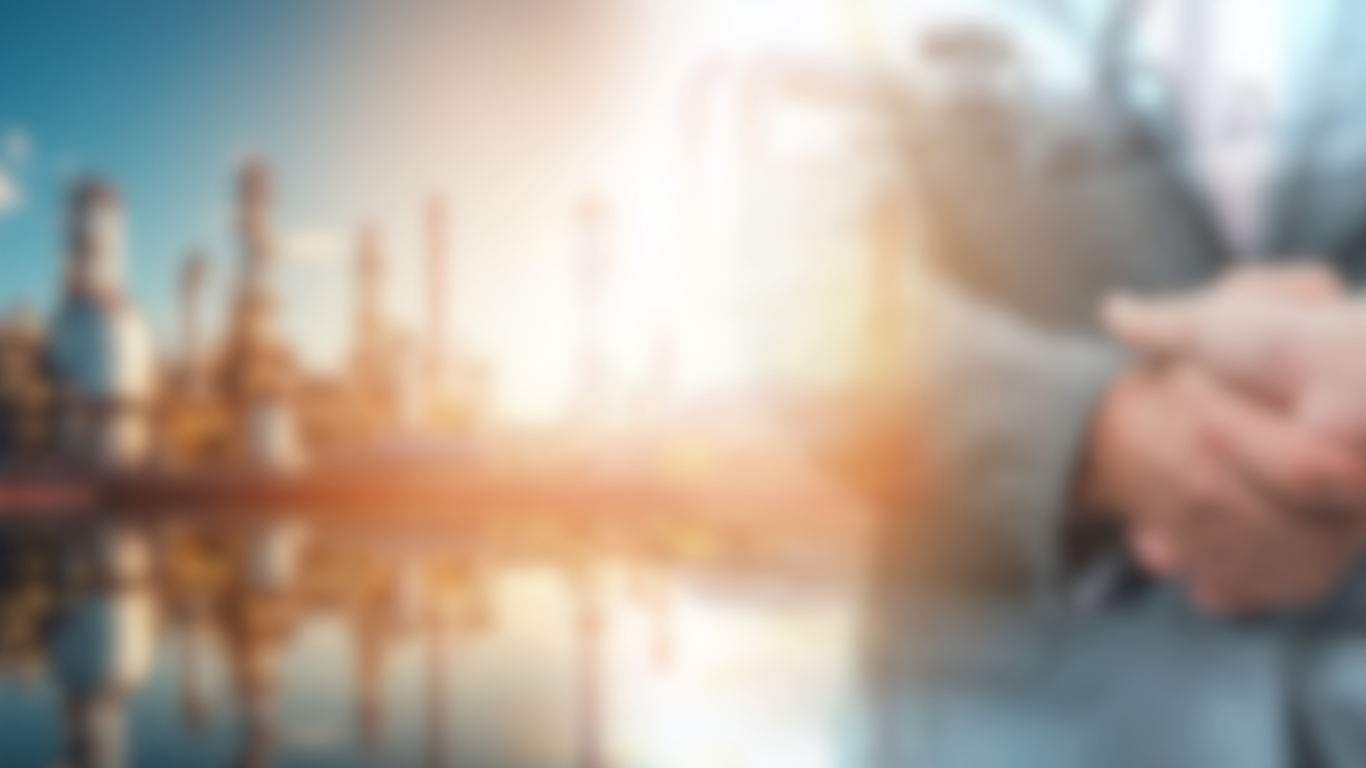
Maintenance Improvement
Tailored, innovative maintenance improvement solutions
Whether you head up a maintenance team, are a maintenance manager, responsible for maintenance planning or an engineer - improving takes flexibility. There has to be a willingness on all sides to think along new lines of maintenance improvement techniques if you want to improve your maintenance operations.
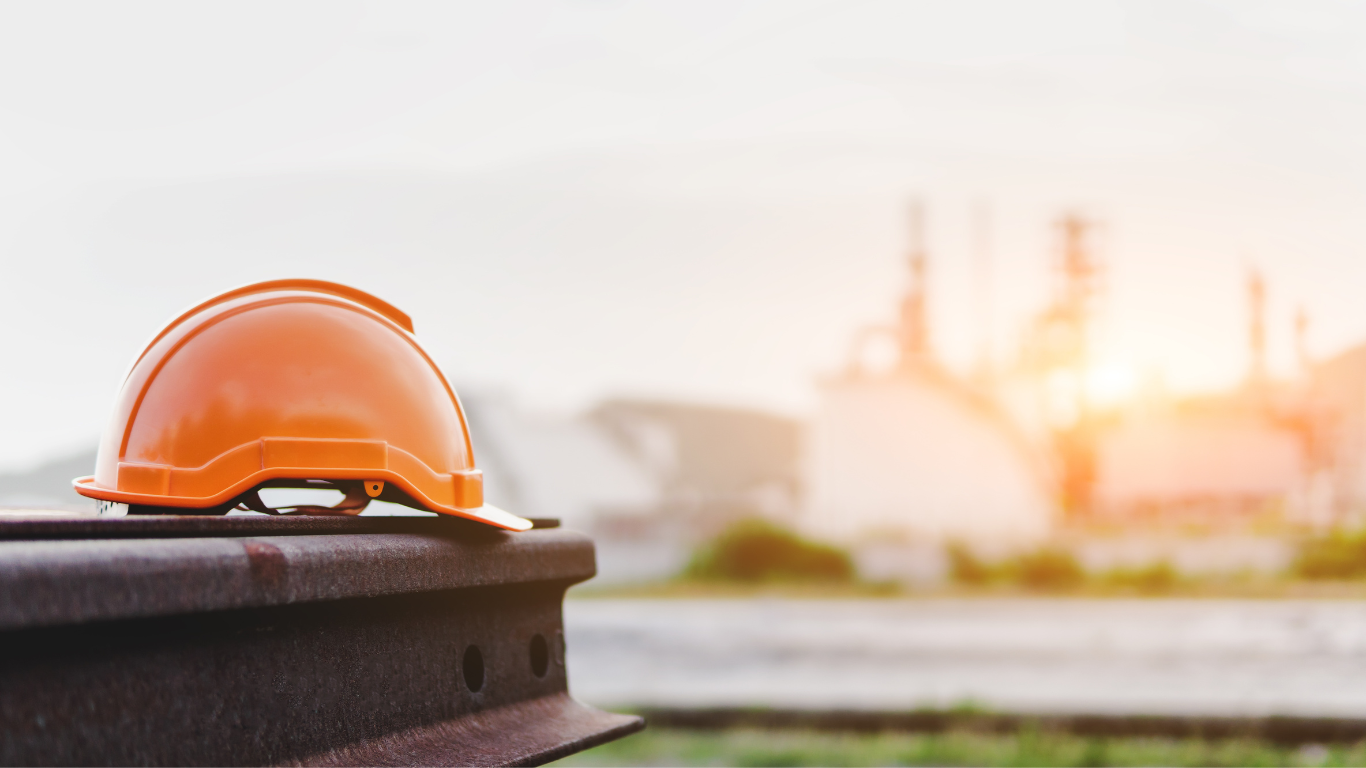
We Can Support You with
All Areas of Maintenance Improvement
1
Asset Base Restructuring
Restructuring asset base, particularly useful for multi-site portfolios enabling comparison and standardisation.
2
Spares Data
Spare parts data cleansing for accuracy and efficiency.
3
CMMS Selection
Choosing and implementing new or improving existing CMMS systems.
4
CMMS Data Integrity
Cleansing data that goes through the CMMS to ensure it provides accurate output.
5
Developing System Hierarchies
Establish system hierarchy for CMMS and software.
6
Maintenance Strategies
Support with new preventative and predictive maintenance regimes.
7
Optimised Spare Parts
Effective spare parts inventory management, processes and stocks.
8
KPI Dashboards
Performance dashboard and KPI’s to drive continuous improvements.
Contract Management
9
Contract management and permit software selection.
Improving maintenance effectiveness to reduce costs is achieved through a structured approach, technology tools and training and coaching of maintenance teams.
No matter which type of maintenance practices, processes and systems you currently have on your site, improvements can be made with a tailored, innovative maintenance improvement plan.
OTHER SERVICES WE PROVIDE:
Maintenance Management
Physical Asset Management
Reliability Management
Spares
Management
Facilities
Management
Are You Looking for New Ways to
Improve Maintenance?
There are many tried and tested methods to improving maintenance practices but many are time and labour intensive. MCP Consulting Group use our 50 years industry experience together with the newest, most innovative technology tools to help you create a new maintenance improvement plan. A plan that is clear, concise and simple to follow. A plan that will provide the improvement you need to meet your targets.
The Rewards of
Improved Maintenance Processes
Effective maintenance planning, scheduling and maintenance work management is critical if you want to take back control over your maintenance activities. Yet implementing an effective maintenance improvement plan is not an easy task, particularly if you are already operating in a reactive operational environment and constantly dealing with the possible failure of equipment. But help is at hand...
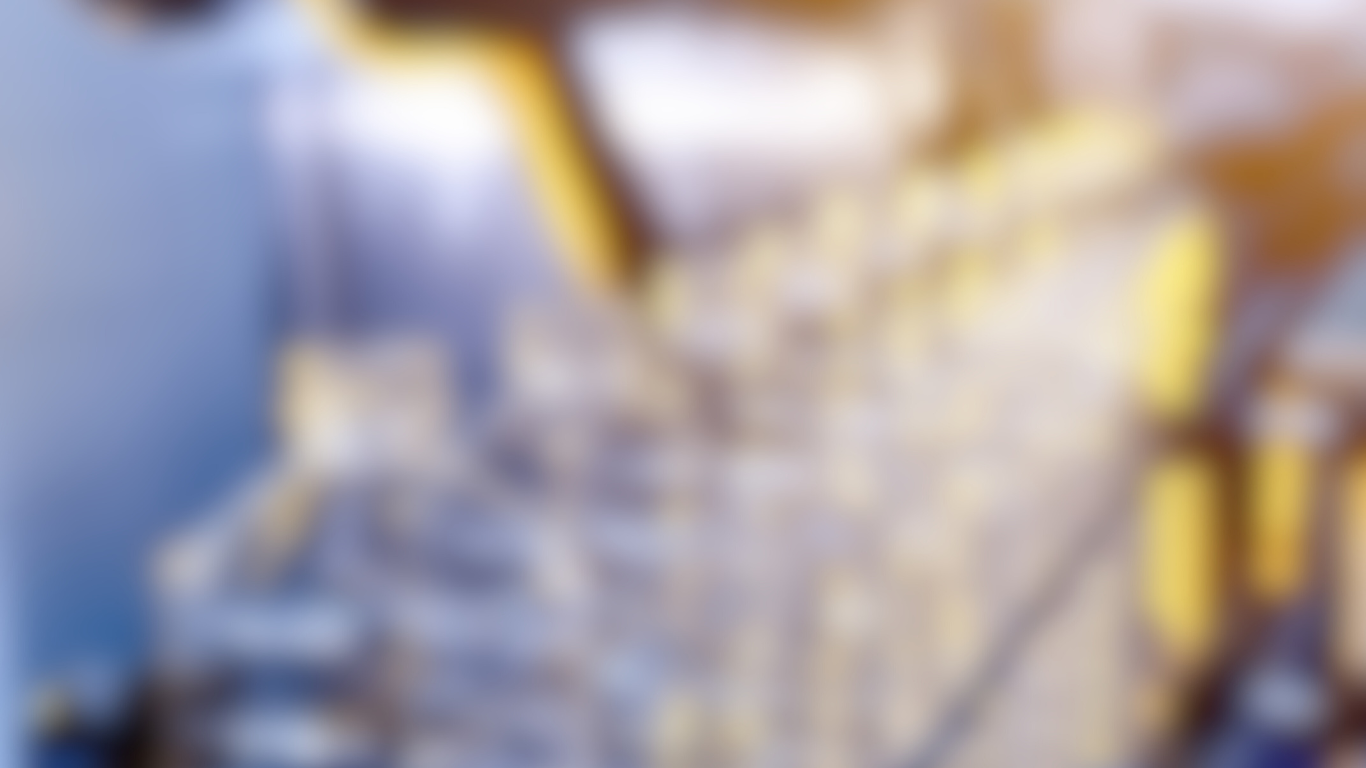
MCP Approach to
Maintenance Improvement
Partnering with You to Deliver Sustainable Maintenance Improvement
At MCP, our approach is practical, collaborative, and proven to deliver results. We work alongside your team to reduce maintenance costs, enhance workforce productivity, and improve the reliability of your assets. Our support is grounded in best practice and tailored to meet your specific operational needs.
We begin with a detailed review of your critical assets, maintenance activities, and CMMS using our proprietary assessment tool, AMIS. This enables us to benchmark performance and identify areas for improvement.
Comprehensive Maintenance Assessment
Insight-Driven Recommendations
Based on a thorough analysis of your current situation, we provide evidence-based, practical recommendations designed to deliver measurable benefits.
Process Definition and Visual Mapping
We clearly define maintenance work management, planning, and scheduling processes. These are documented using straightforward flowcharts and reports that promote clarity and consistency.
Engagement and Alignment
We work closely with your management and maintenance teams to build ownership and consensus around new ways of working, ensuring alignment across departments.
Training Across All Levels
Training is delivered throughout your organisation to ensure everyone understands both the process and the purpose behind it - fostering commitment and compliance.
Operational Collaboration
We engage production, operations, and maintenance leaders to reinforce the importance of cross-functional cooperation in sustaining improvements.
Coaching and Mentoring
On-the-job coaching is provided to planners, supervisors, and engineers, supporting them as new processes are embedded into day-to-day operations.
Barrier Identification and Continuous Refinement
We assist in removing obstacles to implementation and support ongoing refinement of processes to maintain momentum and progress.
Performance Monitoring
We track compliance and quantify improvements using agreed KPIs—helping you demonstrate return on investment and operational benefit.
Embedding a Culture of Continuous Improvement
Our ultimate aim is to help establish a sustainable culture where maintenance is continuously assessed, improved, and aligned with business objectives.
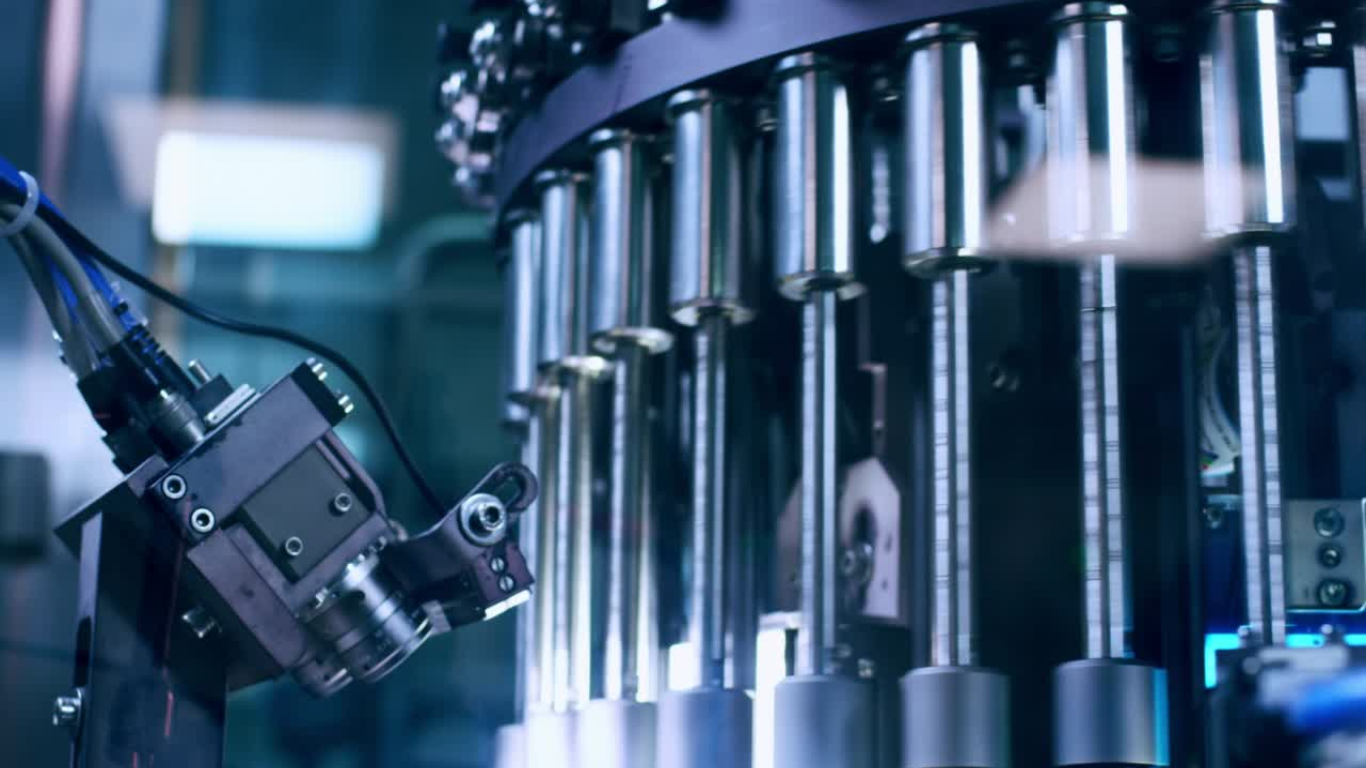
Maintenance Improvement
Explore More
Speak to One of Our
Reduce costs and increase uptime.
Are you ready to achieve more efficient maintenance practices? To find out more about how we can help you establish a robust maintenance improvement programme contact us for an obligation-free discussion.
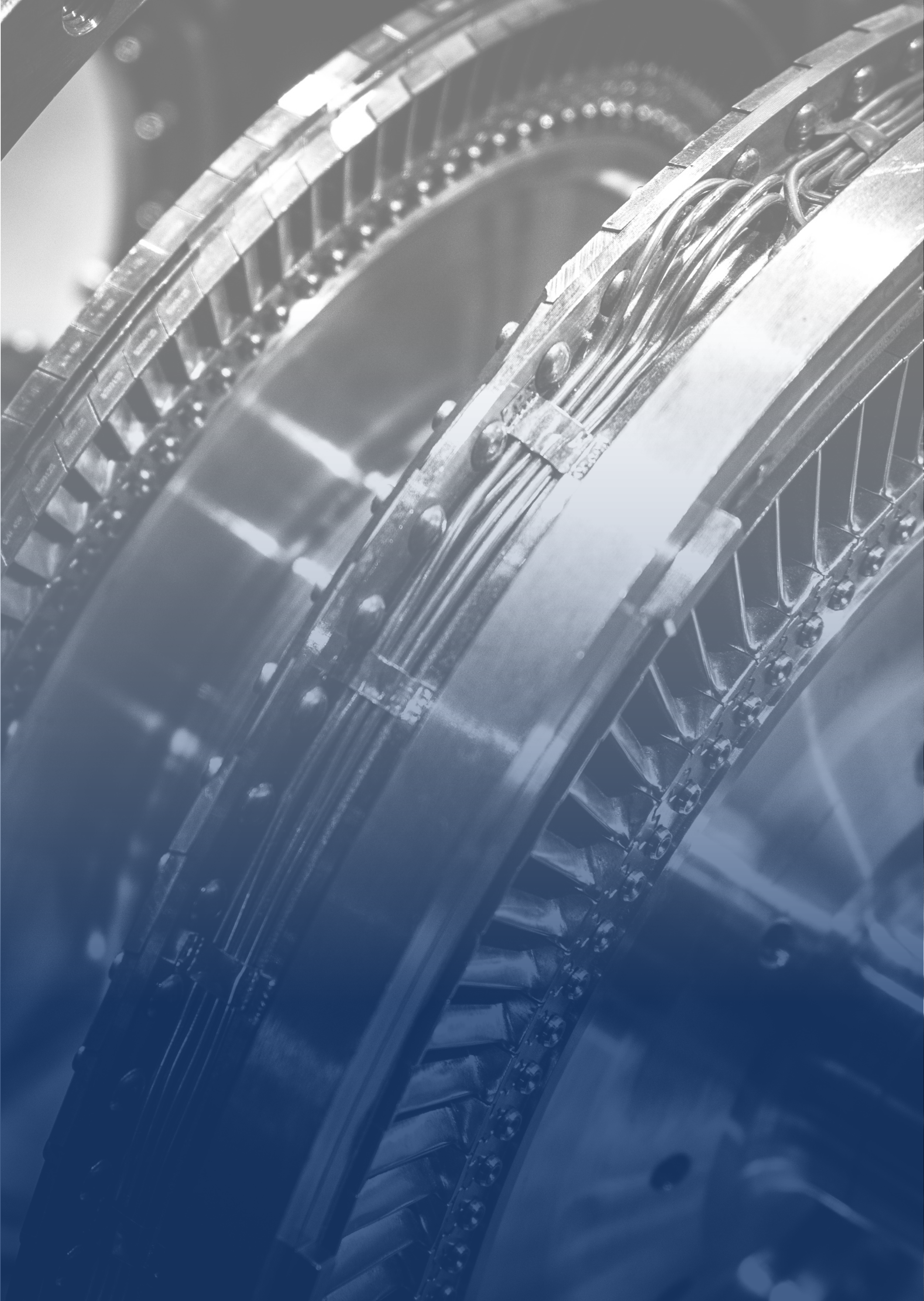
FAQs
-
Continuous improvement is a company culture that encourages all employees to look for ways to enhance the business's operations. This includes suggesting ideas to improve efficiencies, evaluating current processes, and finding opportunities to cut unproductive work.
-
Reactive maintenance, preventive maintenance, predictive maintenance or reliability centred maintenance are the 4 main maintenance programmes. However, there are many different approaches that you can mix and match, depending on your assets, your industry, and the size and experience of your maintenance team. The bottom line, there is "no one size fits all" approach to maintenance. To develop am effective maintenance strategy you have to evaluate and weigh the unique benefits and shortcomings of each strategy, depending on what assets you're working with, what stage of the reliability journey your organisation is at, and the impact of downtime at your facility.
-
The main difference between these two maintenance methods is that preventive maintenance is scheduled on a regular basis, while predictive maintenance is scheduled as needed, based on the asset's current condition. Both approaches rely heavily on data to guide decisions but in different ways. A preventive maintenance (or preventative maintenance) looks at industry averages, checks recommendations from the Original Equipment Manufacturer (OEM) and understanding of best practices. Whereas, a predictive maintenance program uses an asset's actual utilisation and current condition to decide when to perform a maintenance task.
-
An effective maintenance strategy is one that balances cost, reliability, and asset performance. Key indicators include reduced unplanned downtime, improved asset availability, lower maintenance costs over time, and increased planned-to-unplanned work ratios. Regular reviews, performance dashboards, and maintenance KPIs, such as Mean Time Between Failures (MTBF) and Mean Time To Repair (MTTR), can help assess whether your current approach is delivering value.
-
A Computerised Maintenance Management System (CMMS) is a crucial tool for organising, tracking, and optimising maintenance activities. It helps schedule work orders, monitor asset health, manage spare parts inventory, and generate performance reports. When used effectively, a CMMS supports data-driven decision-making, ensures accountability, and provides visibility across maintenance operations—forming the backbone of any continuous improvement programme.