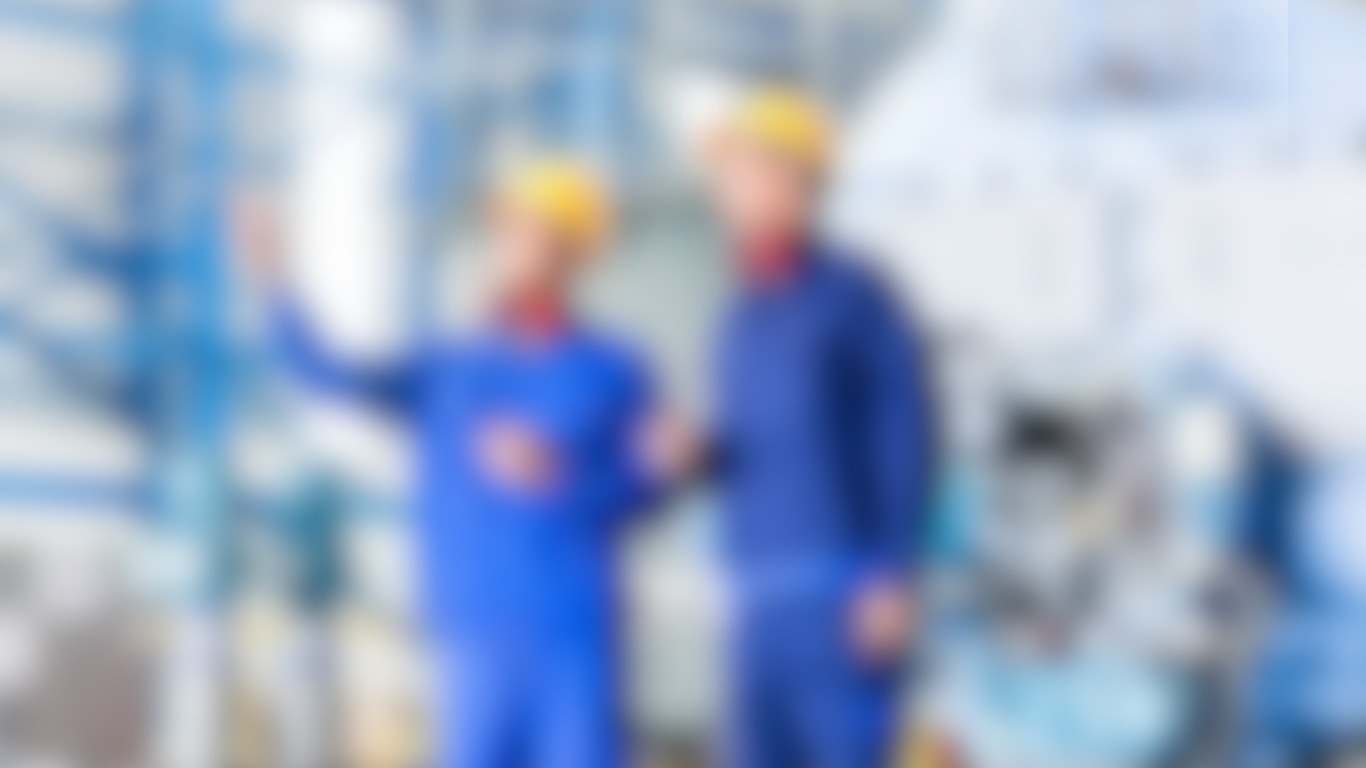
Planned Maintenance Programmes
Ensuring the reliability and efficiency of assets is crucial for any organisation. At MCP Consulting Group, we specialise in developing and optimising Planned Preventive Maintenance (PPM) programmes that are tailored to your operational needs, regulatory requirements, and equipment conditions. Our goal is to create maintenance strategies that are effective, efficient, and aligned with your business objectives.
MAINTENANCE PLANS SUB-CATEGORIES
What are
Planned Maintenance Programmes
Planned Maintenance Programmes involve scheduled maintenance activities designed to prevent equipment failures and extend asset lifespan. These programmes are essential for ensuring operational reliability but must be carefully designed to avoid inefficiencies or redundancies.
At MCP, we work closely with your technicians to develop customised maintenance plans using methodologies such as Failure Modes, Effects, and Criticality Analysis (FMECA), Reliability-Centred Maintenance (RCM), and our proprietary Review of Equipment Maintenance (REM) tools. This comprehensive approach considers regulatory and environmental requirements, historical equipment data, and operating conditions to formulate optimal maintenance strategies.
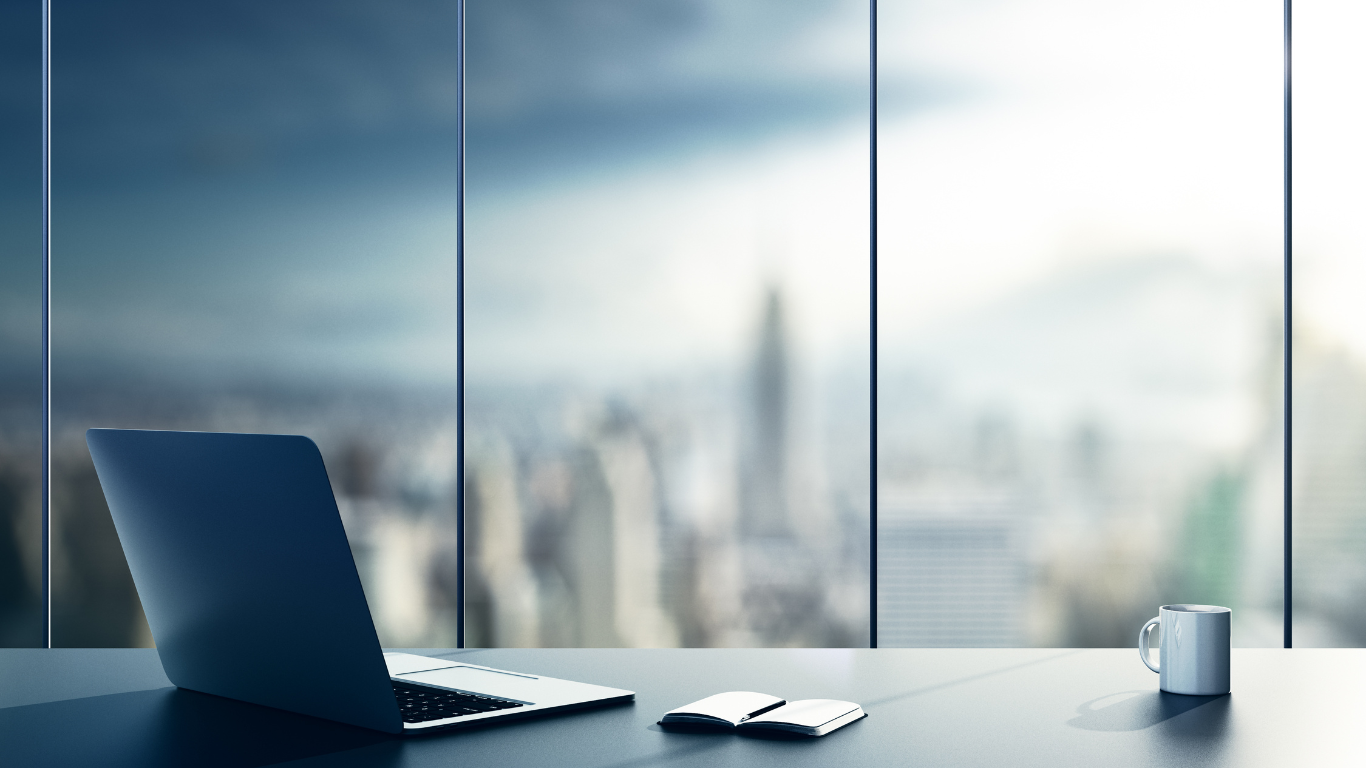
Key Objectives of
Planned Maintenance Programmes
Implement maintenance activities that ensure equipment operates efficiently and without unexpected failures.
1
Enhancing Asset Reliability
Reducing Operational Risks
2
Identify and mitigate potential failure modes to minimise unplanned downtime and associated costs.
Optimising Maintenance Efficiency
3
Develop maintenance plans that are effective yet not overly time-consuming or redundant.
Align maintenance activities with regulatory and environmental standards to maintain compliance and avoid penalties.
4
Ensuring Compliance
Extending Asset Lifespan
5
Perform regular maintenance to prolong the useful life of machinery and infrastructure, thereby maximising return on investment.
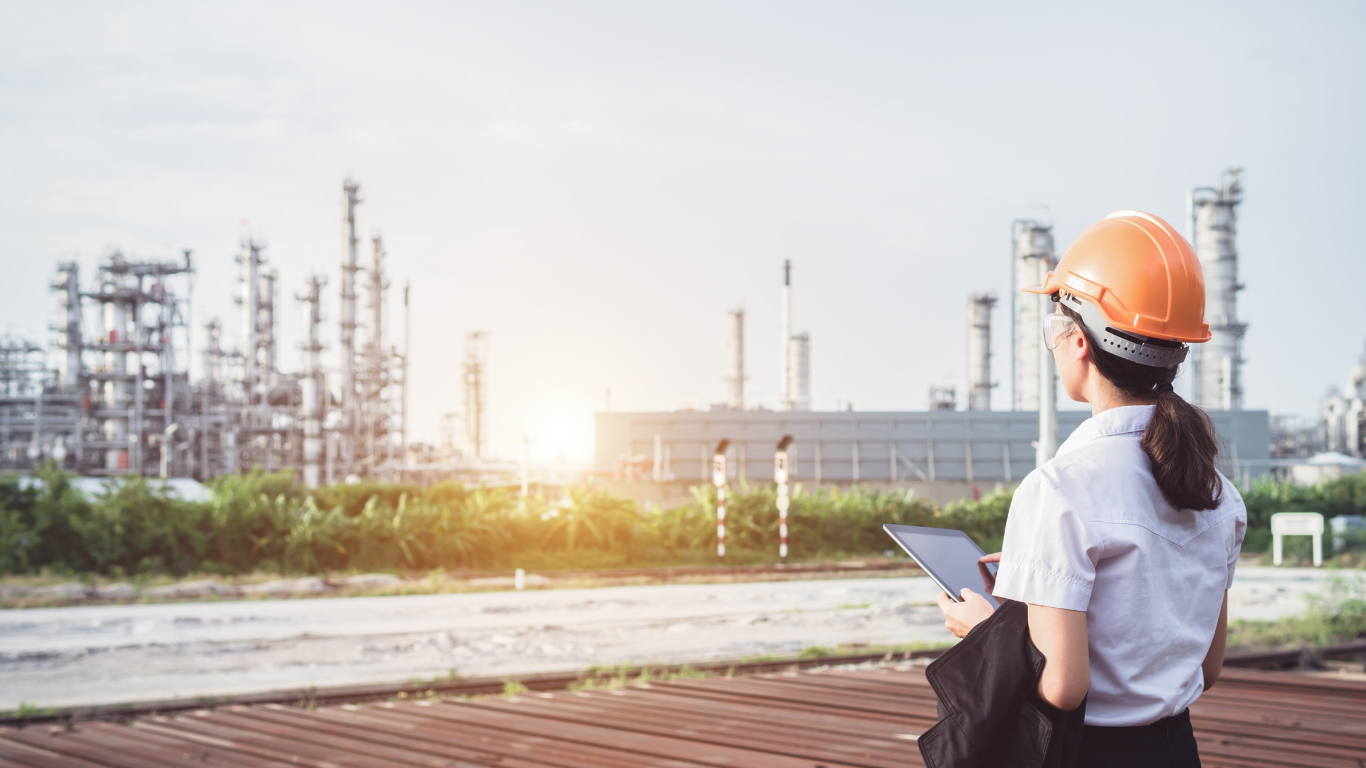
MCP Approach to
Planned Maintenance Programmes
Asset Criticality Assessment
We begin by establishing the relative importance—criticality—of your assets. A formal criticality analysis helps prioritise work, manage risk, and serves as the foundation for developing effective maintenance plans.
Development of Maintenance Strategies
Utilising FMECA or RCM methodologies, our consultants work with your in-house teams to analyse assets at the system or component level, as determined by their criticality. This analysis informs the selection of appropriate maintenance tasks, whether preventive, predictive, or design-out.
Creation of Maintenance Plans and Job Plans
For each critical asset, we develop individual tasks and job plans based on identified failure modes, available maintenance options, and risk assessments. These plans detail the necessary skills and spare parts and are formatted for seamless integration into your Computerised Maintenance Management System (CMMS) or Enterprise Asset Management (EAM) system.
REM Optimisation Process
Our proprietary REM optimisation process is employed to refine your existing PPM programme. This process reviews existing plans and identifies the appropriate preventive, predictive, and design-out tasks, ensuring that your maintenance activities are both effective and efficient.
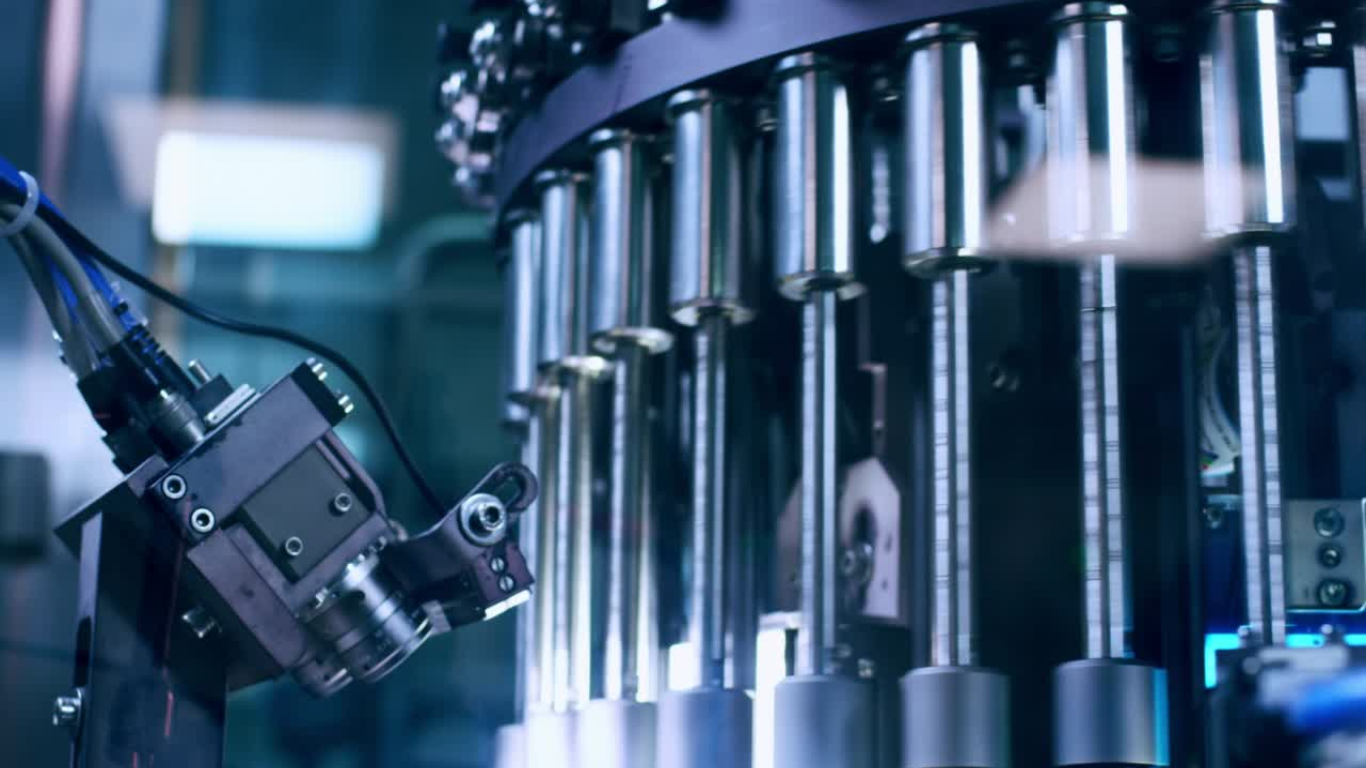
Maintenance Plans
Explore More
Speak to One of Our
Experienced Consultants
If you have any questions or would like to learn more about how MCP can support your organisation with Planned Maintenance Programmes, please get in touch with us.
Our team of consultants is ready to provide tailored solutions to enhance asset reliability, optimise maintenance efficiency, and improve operational performance. Contact us today to discuss your specific requirements.
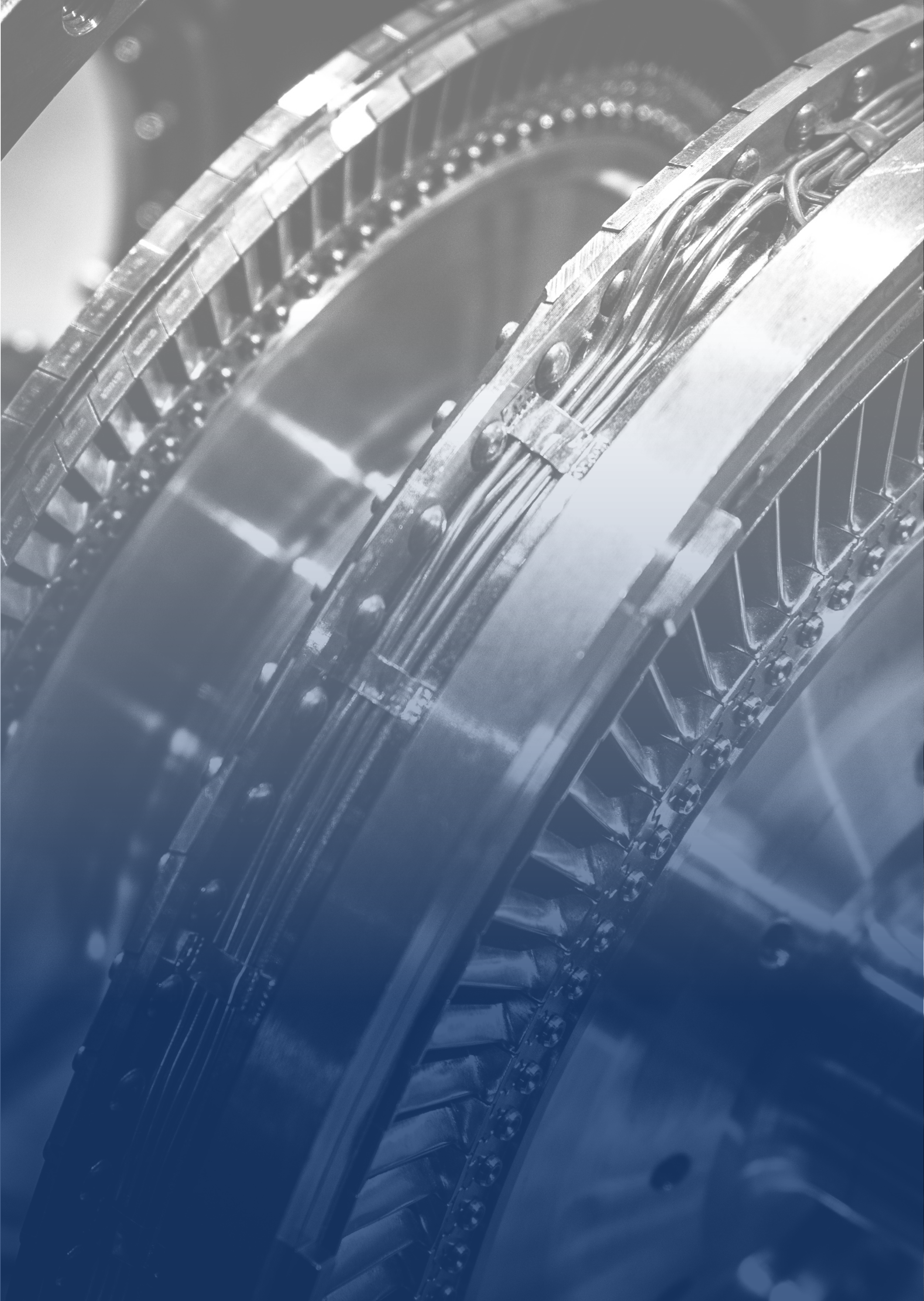
FAQs
-
They are crucial for ensuring asset reliability, reducing unplanned downtime, and extending equipment lifespan.
-
We work with your technicians to develop tailored maintenance plans building on their knowledge and experience using methodologies like FMECA, RCM, and REM, considering factors such as regulatory requirements and historical equipment data.
-
It is MCP's proprietary process that optimises existing maintenance programmes by defining appropriate preventive, predictive, and design-out tasks.
-
Yes, we ensure that all maintenance plans are formatted for seamless integration into your existing systems.