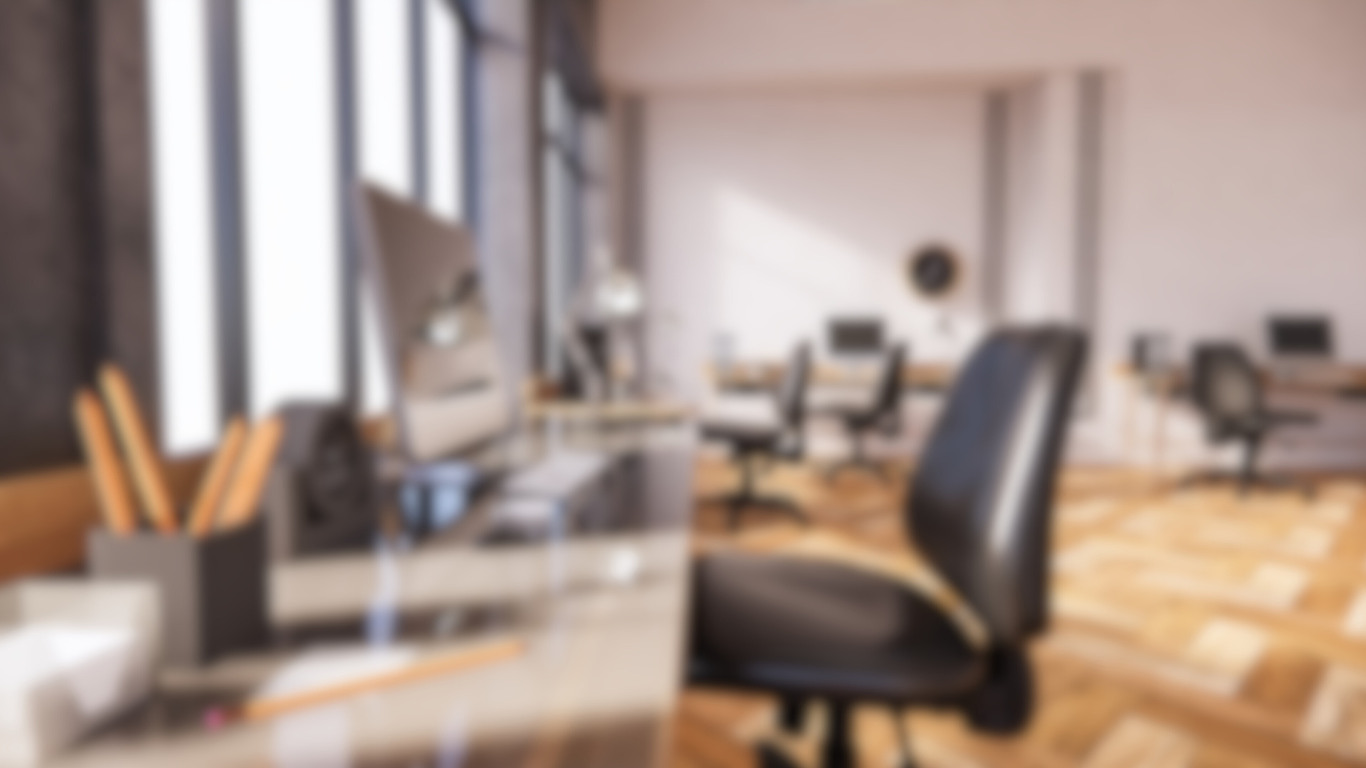
Types of Maintenance
A well-defined Planned Maintenance (PM) strategy is essential for ensuring asset reliability, operational efficiency, and cost control. By structuring maintenance activities based on asset criticality, condition monitoring, and industry best practices, organisations can reduce downtime, extend asset life, and improve compliance with regulatory requirements.
At MCP Consulting Group, we help businesses implement customised planned maintenance programmes that optimise service schedules, resource allocation, and maintenance budgets.
MAINTENANCE LIFE PLANS SUB-CATEGORIES

What are the
Maintenance Types
Planned maintenance refers to scheduled maintenance activities designed to prevent unexpected failures and optimise asset performance. MCP helps organisations define the right mix of planned maintenance types to maximise efficiency and cost-effectiveness.
PLANNED PREVENTATIVE MAINTENANCE (PPM)
1
Scheduled maintenance tasks performed at regular intervals to prevent failures (e.g., HVAC servicing, fire safety checks, lift inspections).
CORRECTIVE MAINTENANCE (CM)
2
Repairs made after a fault is detected but before asset failure occurs (e.g., fixing a leaking pipe before it bursts).
RELIABILITY CENTERED MAINTENANCE (RCM)
3
Prioritises maintenance based on asset criticality and failure risks, ensuring that high-risk assets receive more attention while non-critical assets receive minimal intervention.
RISK-BASED MAINTENANCE (RBM)
4
A structured data-driven strategy that identifies the most effective maintenance approach based on asset failure modes and operational impact (common in critical building systems).
Tools to determine maintenance types:
PREDICTIVE MAINTENANCE (PdM)
Uses IoT sensors, real-time monitoring, and data analytics to predict failures before they happen (e.g., condition monitoring of chillers or generators).
CONDITION-BASED MAINTENANCE (CBM)
Maintenance performed only when indicators show asset deterioration, similar to PdM but without advanced AI-driven analytics.
Other Key FM Maintenance Types:
REACTIVE MAINTENANCE (RUN-TO-FAILURE
Maintenance only performed after an asset fails, typically for non-critical assets (e.g., replacing a broken lightbulb).
Focuses on reducing energy consumption and improving environmental efficiency through maintenance (e.g., optimising HVAC performance to cut energy waste).
SUSTAINABILITY-DRIVEN MAINTENANCE
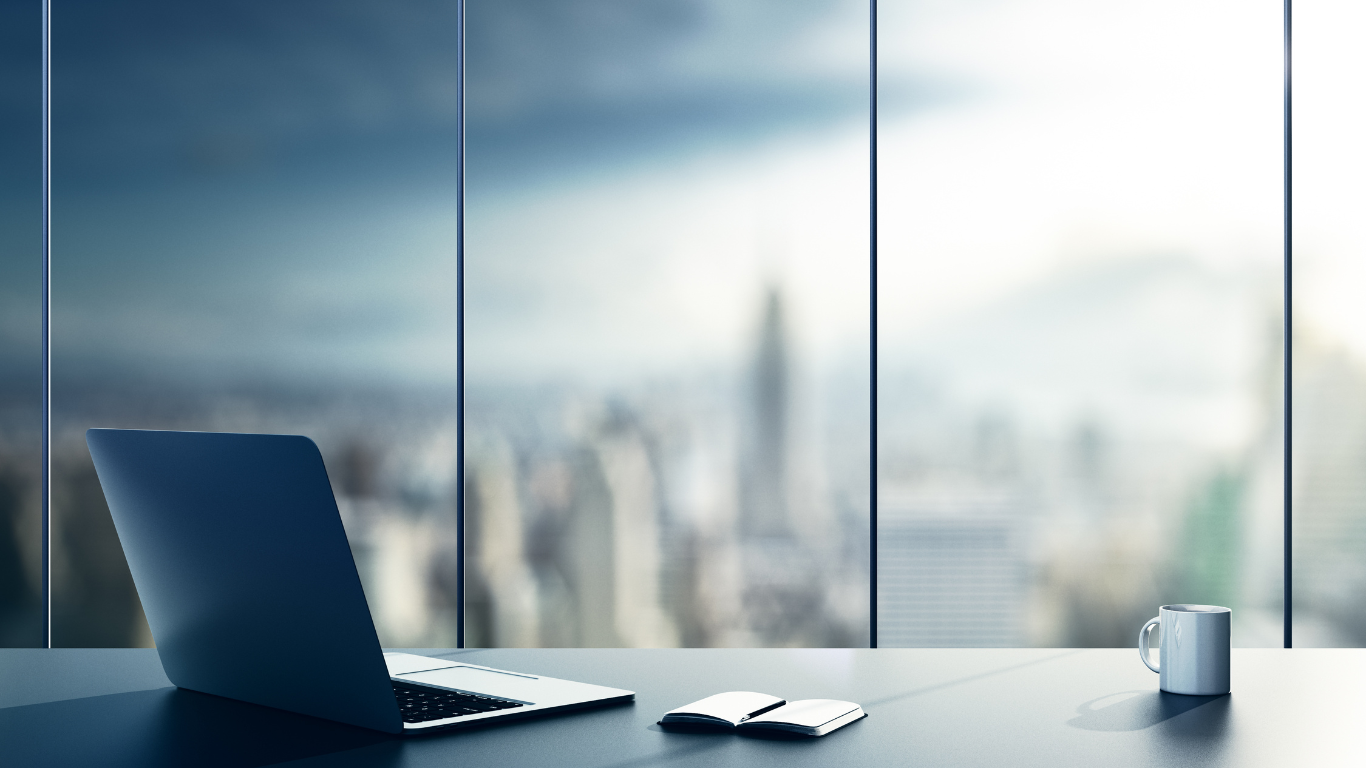
Key Objectives of
Planned Maintenance Types
Implementing structured maintenance tasks and schedules to minimise unplanned breakdowns and disruptions.
1
Reducing Equipment Downtime and Failures
Extending Asset Lifespan
2
Ensuring regular servicing and condition monitoring to prolong the operational life of critical assets.
Optimising Maintenance Resources
3
Allocating workforce, spare parts, and financial resources efficiently to reduce unnecessary costs.
Ensuring facilities meet statutory maintenance regulations and health & safety standards.
4
Improving Compliance and Safety
Enhancing Energy Efficiency and Sustainability
5
Using planned maintenance strategies to reduce energy consumption and environmental impact.
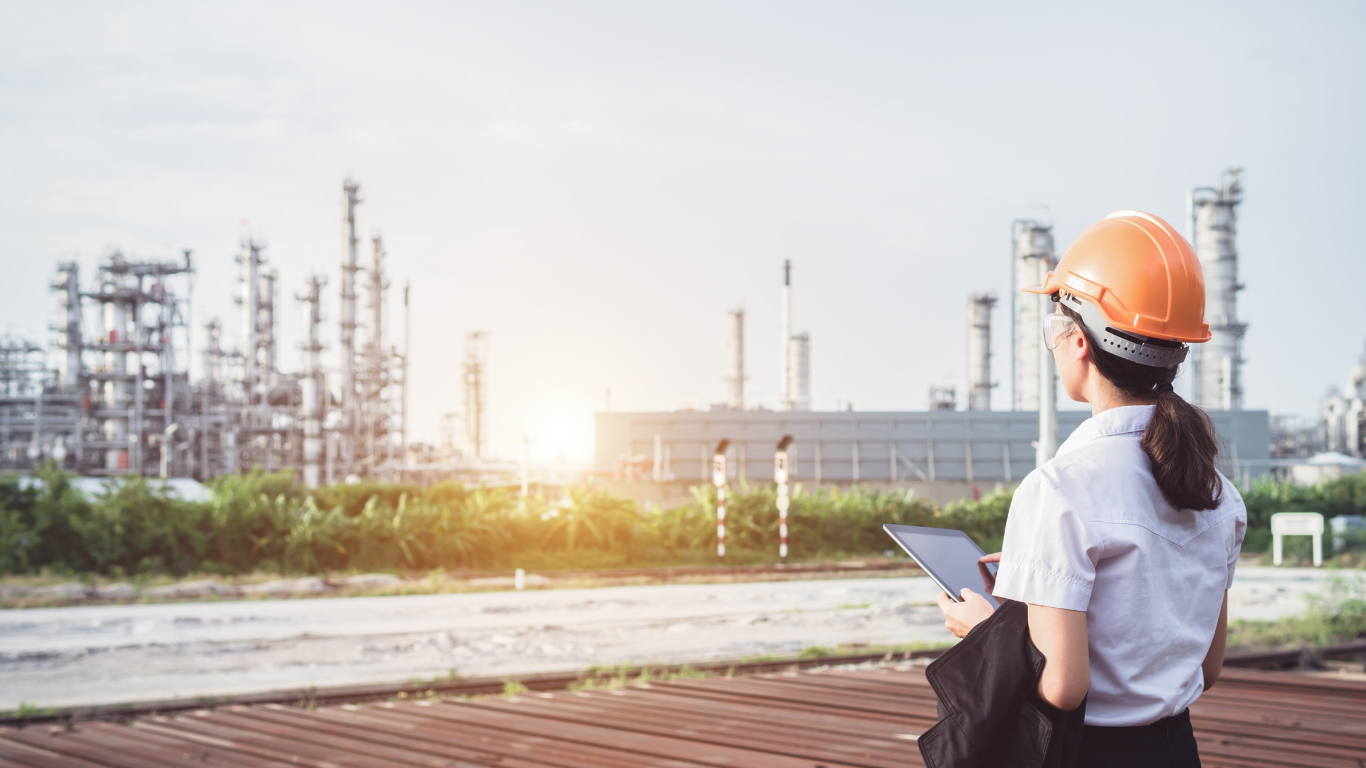
MCP Approach to
Choosing Maintenance Types
Maintenance Strategy Development
We work with organisations to define and implement the most effective mix of planned maintenance types, aligning maintenance activities with business goals and regulatory requirements.
Customised Preventive and Predictive Maintenance Plans
MCP helps businesses design preventive and predictive maintenance programmes, ensuring that maintenance is proactive rather than reactive.
Risk and Reliability Analysis
Our consultants conduct risk-based and reliability-centred assessments to determine the optimal level of maintenance required for each asset.
Integration with CMMS and Digital Solutions
We support the selection and implementation of Computerised Maintenance Management Systems (CMMS), allowing organisations to track maintenance schedules, automate servicing, and monitor asset health in real time.
Continuous Performance Monitoring and KPI Tracking
MCP assists businesses in establishing Key Performance Indicators (KPIs) to monitor maintenance effectiveness and drive ongoing process improvements.
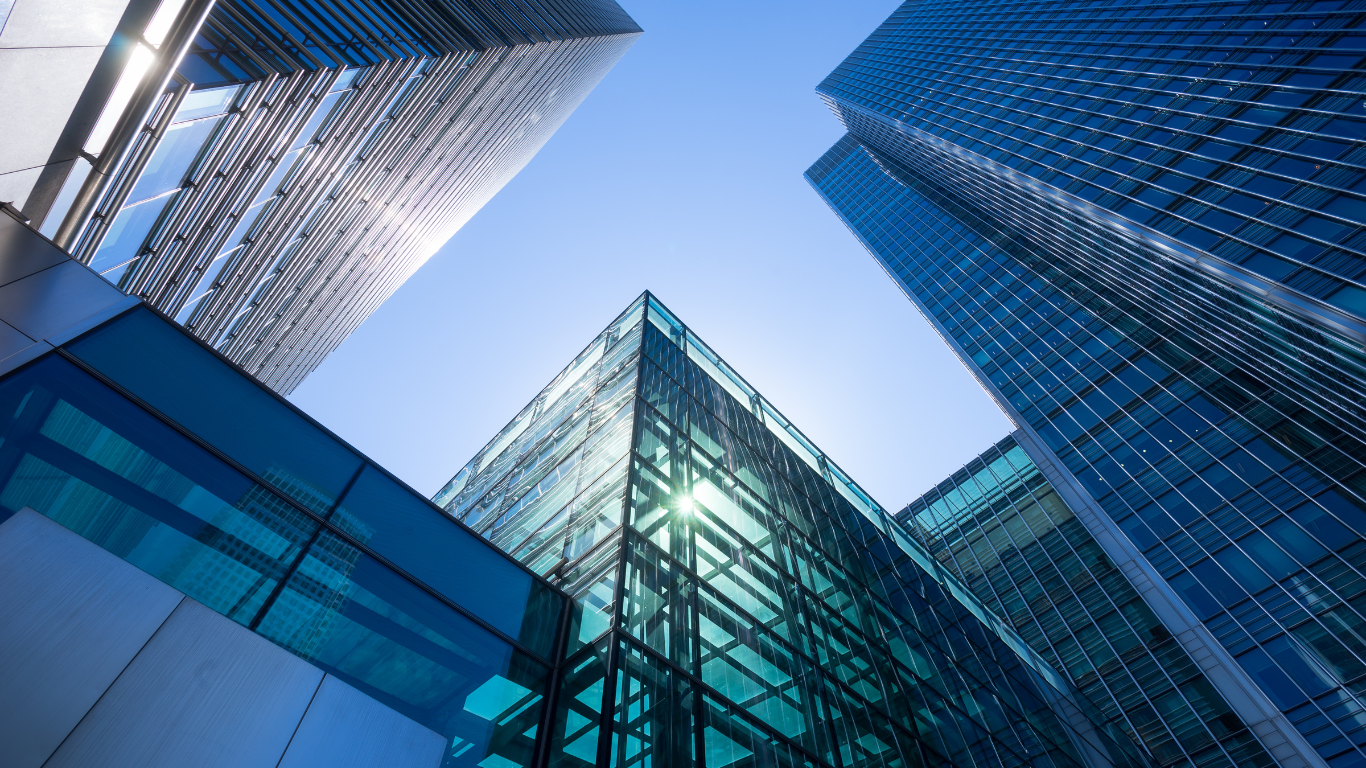
Maintenance Life Plans
Explore More
Speak to One of Our
Facilities Management Consultants
If you have any questions or would like to learn more about how MCP Consulting Group can support your organisation with choosing Maintenance Types, please get in touch with us.
Our team of consultants is ready to provide tailored solutions to optimise FM maintenance planning, reduce downtime, and improve asset performance. Contact us today to discuss your specific requirements.
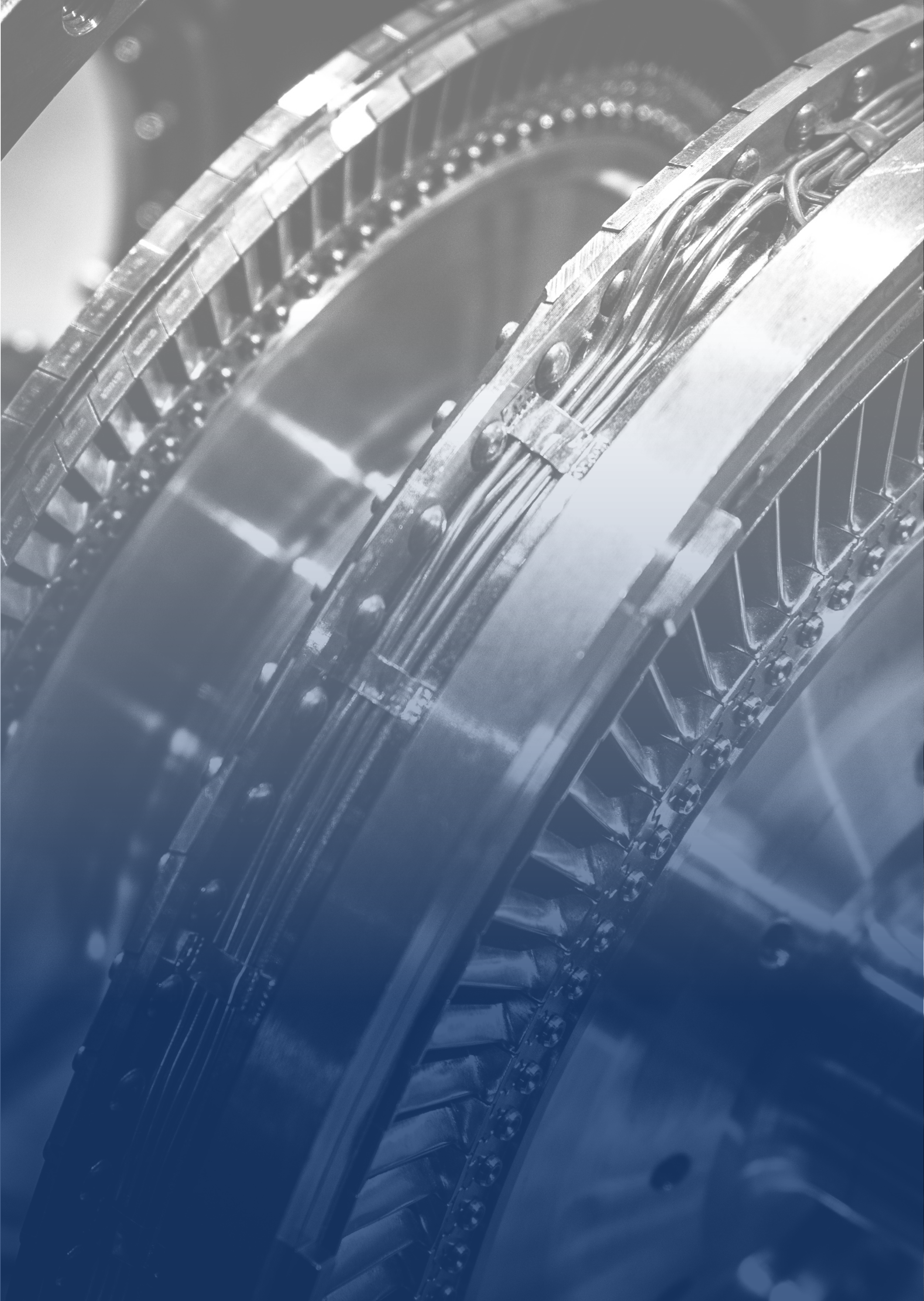
FAQs
-
Preventive maintenance follows a fixed schedule, whereas predictive maintenance uses real-time condition monitoring to determine servicing needs.
-
MCP helps organisations assess asset criticality, relative business importance, failure risks and operational needs to design customised maintenance strategies.
-
Yes, by preventing unexpected failures and optimising asset performance, planned maintenance reduces costly emergency repairs and downtime.
-
Regular servicing and predictive analytics help reduce energy waste, extend equipment life, and support sustainability initiatives.
-
CMMS, IoT sensors, and AI-driven analytics allow organisations to automate scheduling, improve accuracy, and optimise maintenance workflows.