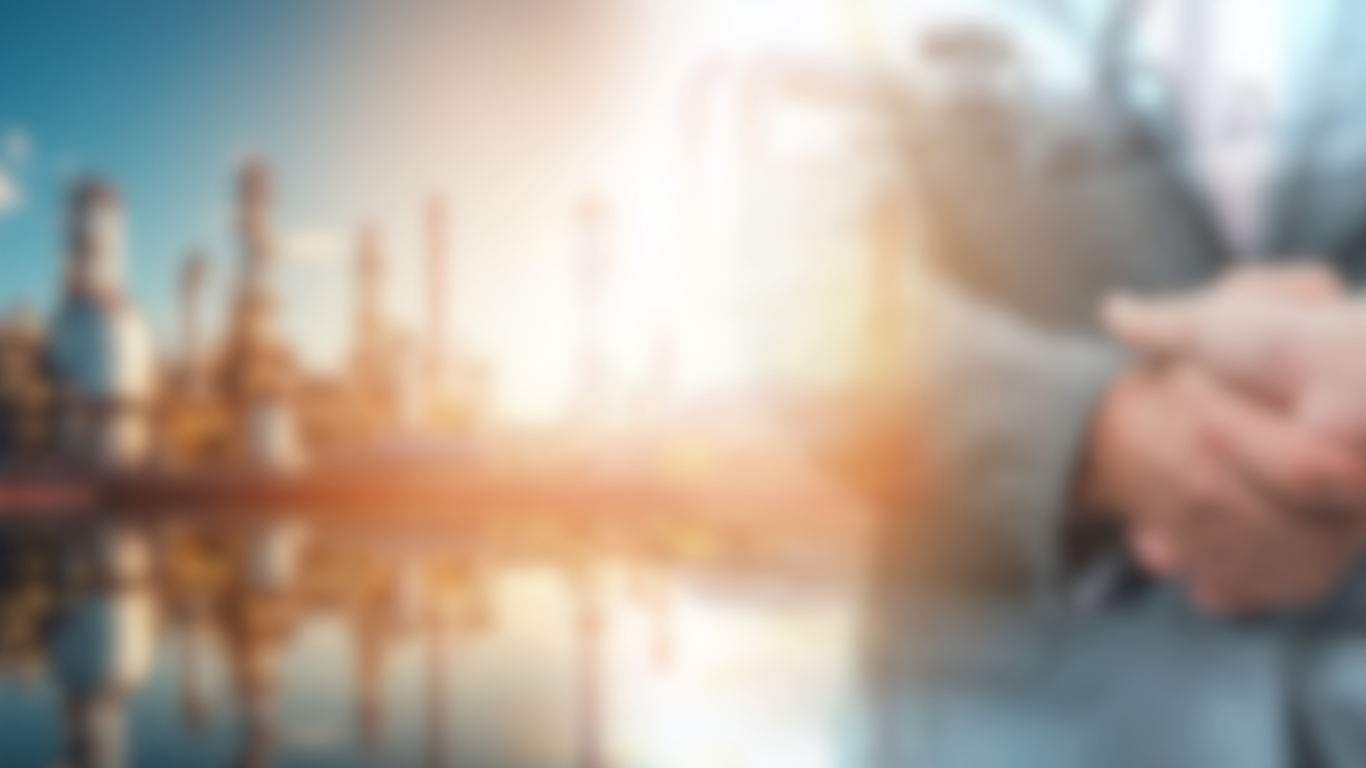
Reliability Improvement
Tailored, innovative reliability improvement solutions
Improving reliability in your organisation requires the right decisions being made to optimise the delivery of value. The objective is to ensure the optimised balance between reliability, availability, maintainability and safety of all assets, at optimal cost.
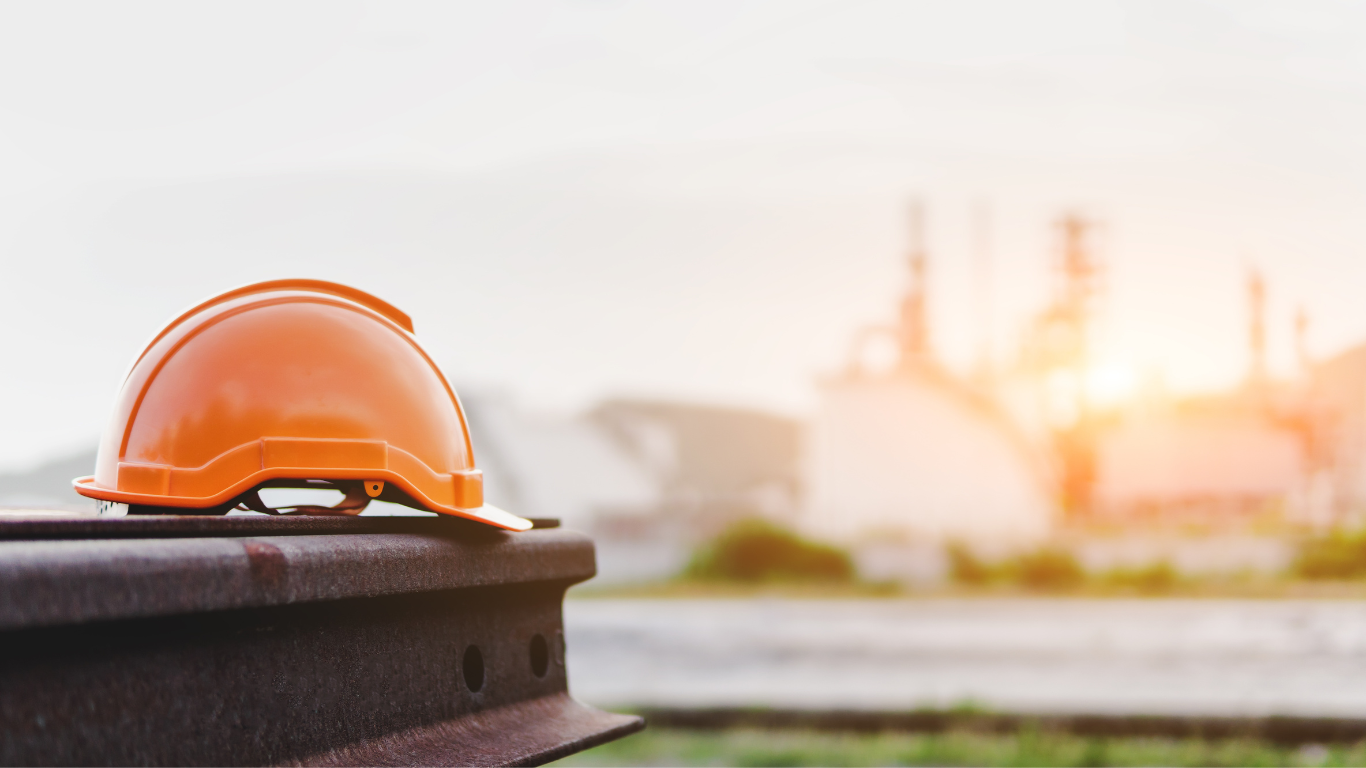
We Can Support You with
All Areas of Reliability Improvement
1
Data Cleansing
We begin by cleansing and validating your asset and maintenance data to ensure that decision-making is based on reliable, meaningful information.
2
Defining Asset Hierarchies
A well-structured asset hierarchy is fundamental to reliability. We work with your team to define a logical, standardised structure that supports effective maintenance planning and reporting.
3
Establishing Performance Indicators
We help identify and implement key reliability metrics—such as MTBF, MTTR, and availability - supported by dashboards that provide real-time visibility of performance.
4
CMMS or CAFM Selection
Whether selecting a new system or optimising an existing one, we assist in choosing the right Computerised Maintenance Management System (CMMS) or Computer-Aided Facilities Management (CAFM) solution to support your reliability goals.
5
Development of Maintenance Programmes
We help design maintenance strategies tailored to asset criticality and performance requirements - balancing preventive, predictive and condition-based approaches for maximum efficiency.
6
Asset Condition Surveys
Our condition surveys provide a detailed understanding of asset health and performance, enabling informed planning and early identification of reliability risks.
7
Refurbishment and Replacement Planning
Using a lifecycle-based approach, we determine the optimum timing for asset refurbishment or replacement - helping you maximise value while avoiding costly failures.
Reliability improvement requires reliability optimisation, criticality and condition of the assets by using the most appropriate tools and techniques for supporting the development and revision of maintenance plans. Technology innovations are driving businesses to transform the traditional way of work in reliability maintenance using digitalisation, and the concepts of the Industrial Internet of Things (IIoT). This can utilise predictive maintenance and failure predictions which contribute to managing risk and improving cost, performance, quality and safety.
No matter which type of processes and practices you follow within your organisation, reliability increases can be made with a tailored, innovative reliability improvement plan.
OTHER SERVICES WE PROVIDE:
Maintenance Management
Physical Asset Management
Reliability Management
Spares
Management
Facilities
Management
Are You Looking for New Ways to
Improve Your Reliability?
There are many tried and tested methods to improve reliability but many are time and labour intensive. MCP Consulting Group use our 50 years industry experience, together with the newest, most innovative technology tools to help you create a new reliability improvement plan. A plan that is clear, concise and simple to follow. A plan that will provide the reliability levels you need to meet your targets.
The Rewards of
Improved Reliability
Our structured approach to reliability improvement consistently delivers measurable value for our clients. By focusing on both technical performance and organisational alignment, we help businesses achieve greater efficiency, cost savings, and long-term asset resilience.
Below are just some of the tangible and intangible benefits our clients experience:
TANGIBLE BENEFITS
Increased asset uptime, resulting in improved operational efficiency and output
Reduced annual maintenance expenditure through optimised maintenance strategies
Lower inventory levels, by aligning spare parts with real maintenance needs
Capital project avoidance, with enhanced asset performance negating the need for major investment - often saving over £1 million
INTANGIBLE BENEFITS
Stronger cross-functional collaboration, fostering better teamwork between maintenance, operations, and project teams
Improved understanding of asset capability, leading to better operational decisions and equipment usage
Enhanced utilisation of maintenance skills, enabling technicians to focus on prevention rather than reactive fixes
Greater awareness of Early Equipment Management (EEM) requirements, improving long-term project and asset outcomes
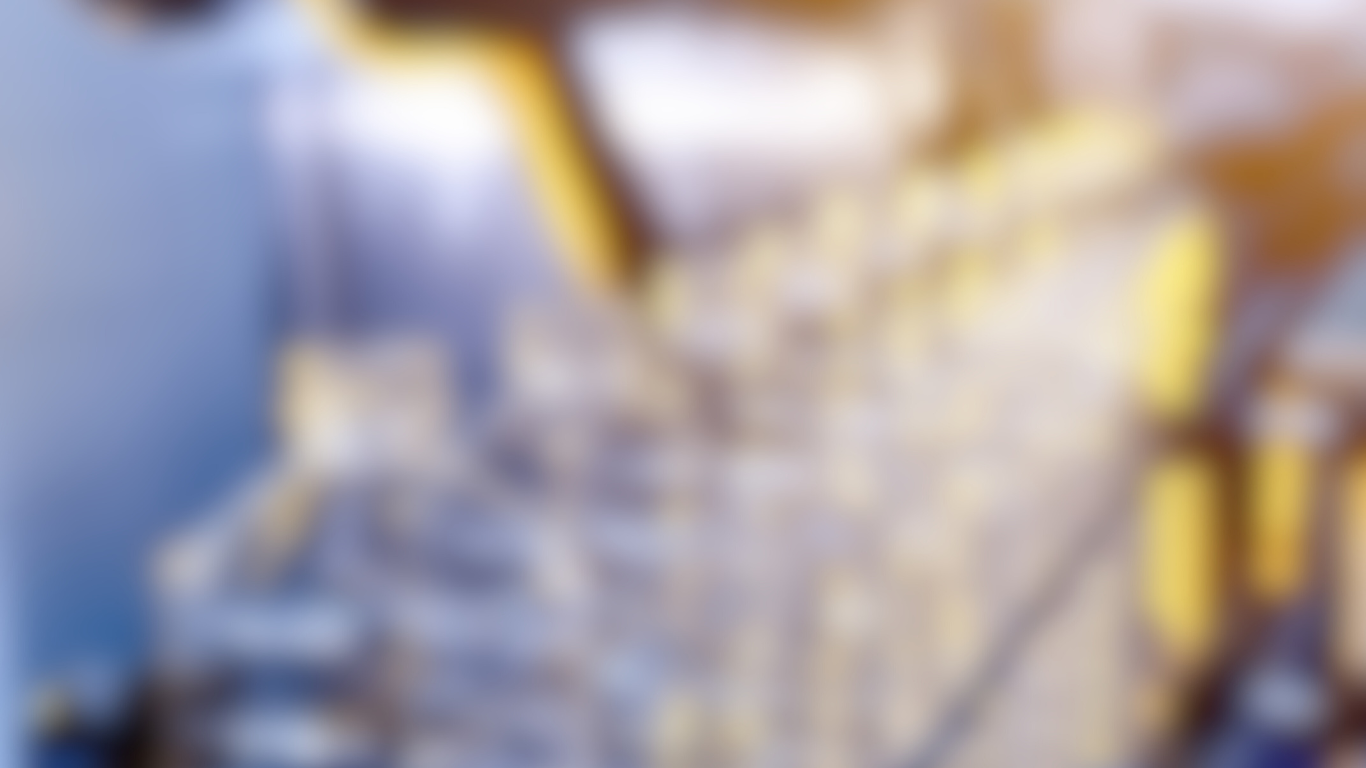
MCP Approach to
Reliability Improvement
A Structured, Holistic Method for Enhancing Asset Reliability
At MCP, we deliver reliability improvement programmes using a comprehensive, top-down and bottom-up methodology. Our approach ensures that every contributing factor, whether technical, operational or cultural, is carefully assessed and addressed. We work closely with your teams to deliver measurable, sustainable improvements across both existing operations and new installations. Here’s how:
We begin by identifying assets with poor reliability, benchmarking current performance against operational expectations and business needs.
Asset Performance and Reliability Review
Operational Standards Assessment
We assess operating standards and related processes to understand whether current practices support or hinder reliable asset performance.
Engineering Practices and Observations
Our team observes engineering activities first-hand to identify any immediate maintenance issues or gaps in best practice.
OEM and Manufacturer Standards Comparison
We review manufacturer documentation to ensure current maintenance practices align with—or appropriately deviate from—OEM recommendations.
Failure History and Trend Analysis
We analyse historical failure data to uncover root causes, recurring issues, and hidden risks that may be undermining asset reliability.
Evaluation of Technical Maintenance Methods
We assess whether existing maintenance strategies and techniques are fit for purpose and delivering the desired outcomes.
Risk-Based Maintenance Review
A structured, risk-based review of asset criticality and failure consequences helps prioritise maintenance tasks for maximum impact.
Team Engagement and Collaboration
We engage with maintenance, operations and project personnel throughout the process to ensure improvements are realistic, understood, and embedded.
Reliability Improvement Planning
Once the assessment is complete, we provide a detailed reliability improvement plan, tailored to your specific needs and business objectives.
Implementation Support and Future-Proofing
We don’t stop at recommendations. MCP supports you through the implementation phase, offering staff training, on-site guidance, and advice on how to future-proof your reliability strategy, whether through continuous improvement planning or the adoption of technologies for condition monitoring and predictive maintenance.
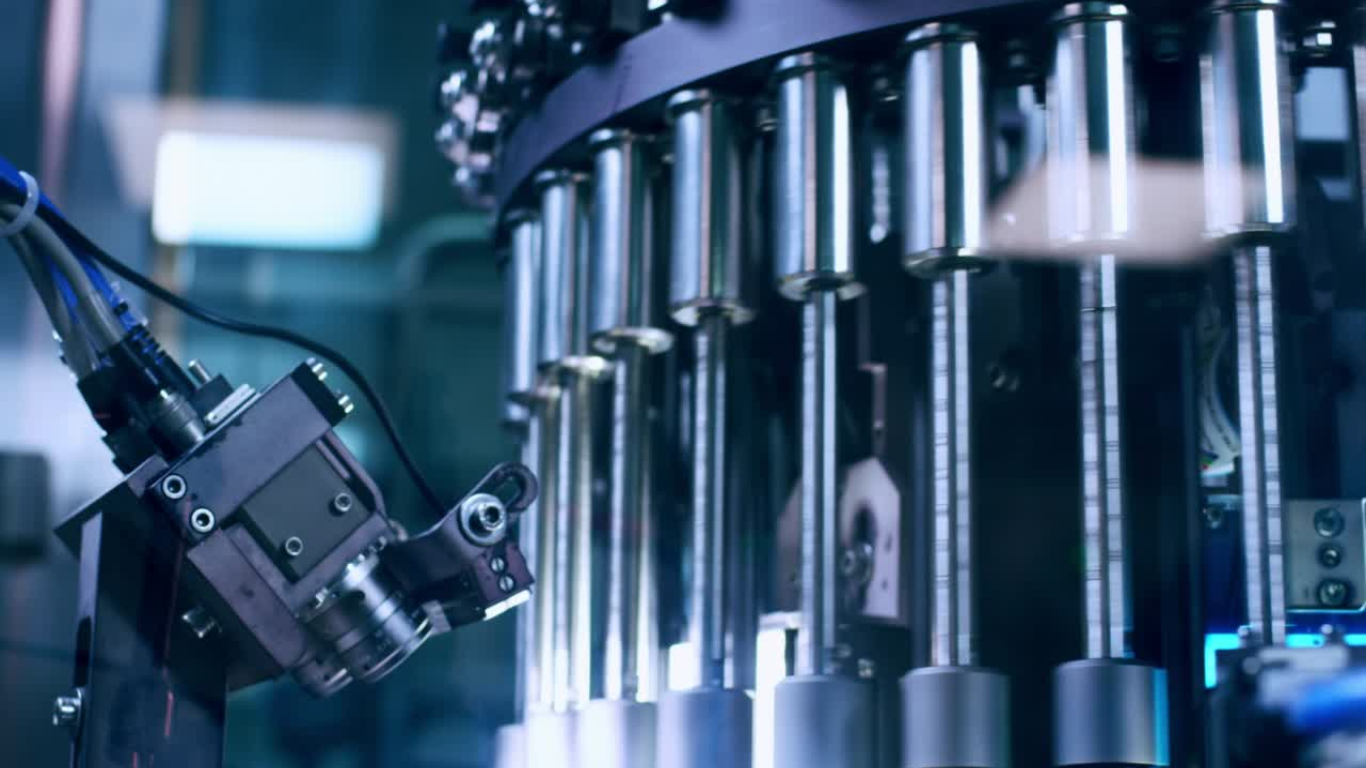
Reliability Improvement
Explore More
Speak to One of Our
Reduce Downtime and Improve Equipment Reliability
Are you ready to achieve your reliability improvement goals?
Whether you're facing persistent breakdowns, inconsistent asset performance, or unclear maintenance priorities, MCP can support you in establishing a robust and sustainable improvement programme.
Contact us today for an obligation-free discussion with one of our experienced consultants and take the first step towards greater reliability and operational performance.
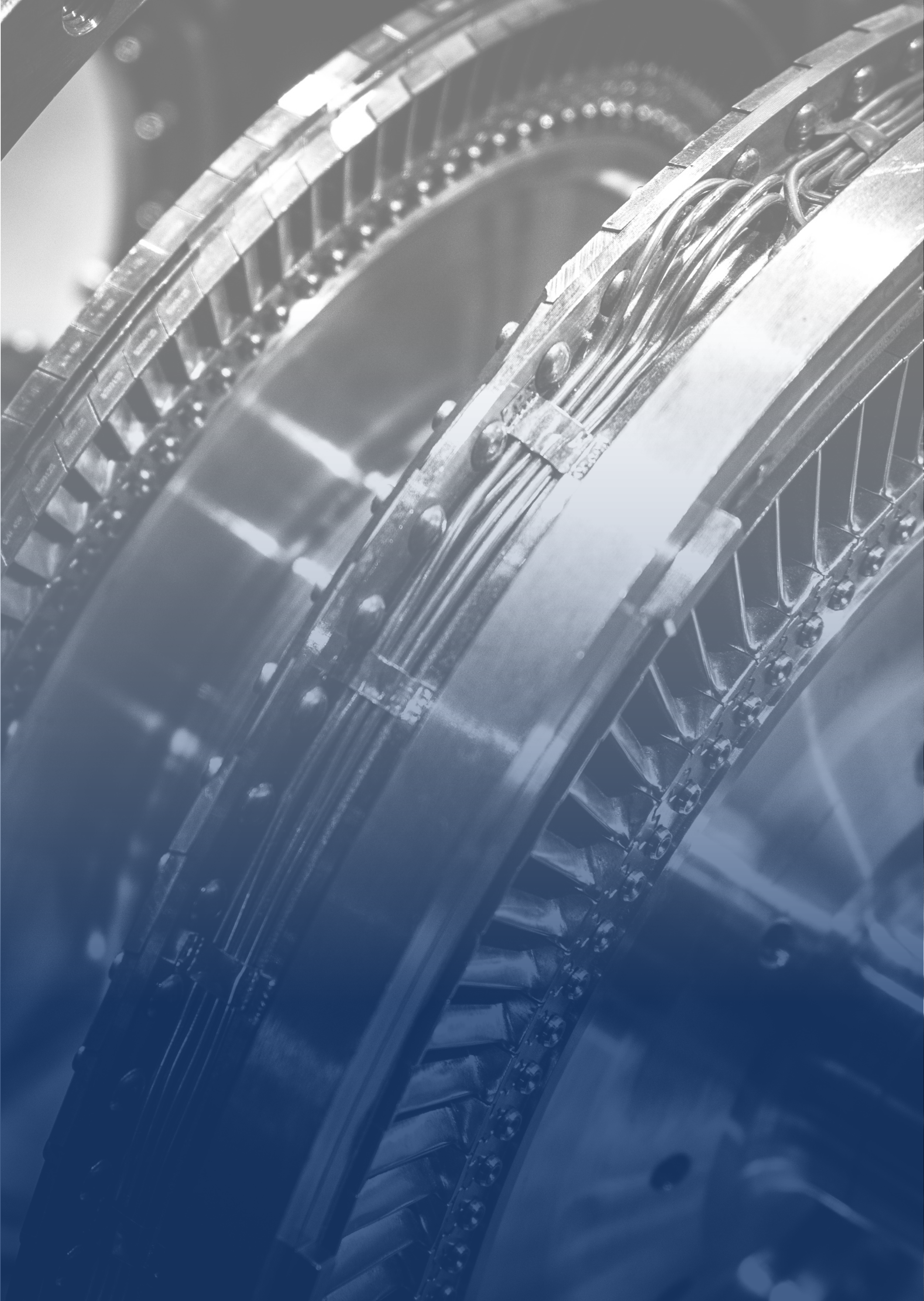
FAQs
-
There are several proven methodologies, each addressing different aspects of asset performance and risk. These include:
Failure Mode and Effects Analysis (FMEA): Identifies how components or systems may fail and the consequences of those failures.
Failure Modes, Effects and Criticality Analysis (FMECA): Builds on FMEA by ranking failures in terms of severity.
Reliability Centred Maintenance (RCM): Develops preventive maintenance strategies based on safety, environmental, and economic priorities.
Planned Maintenance Optimisation (PMO): Streamlines maintenance routines to reduce cost and inefficiencies (methods may vary by vendor).
Root Cause Analysis (RCA): Identifies underlying causes of recurring faults and implements long-term solutions.
Reliability, Availability and Maintainability (RAM) analysis: Assesses system capabilities and highlights risks of production loss.
Review of Existing Maintenance (REM): Evaluates current maintenance strategies to ensure they remain fit for purpose.
-
Key performance indicators include:
Mean Time Between Failure (MTBF): Average time between system failures.
Mean Time to Repair (MTTR): Average time required to repair an asset.
Availability: The percentage of time an asset is ready for use.
These metrics provide valuable insights into both reliability and maintenance effectiveness.
-
A variety of technical and operational elements influence reliability, including:
Poor equipment design
Manufacturing or assembly defects
Inconsistent maintenance practices
Environmental stressors (temperature, humidity, dust)
Improper usage or overloading
Natural wear and tear
-
Reliability Centred Maintenance (RCM) follows a structured and standardised process, incorporating FMEA or FMECA, and is typically used in safety-critical or complex environments.
Planned Maintenance Optimisation (PMO), on the other hand, is more flexible and often used in less regulated environments. PMO aims to streamline maintenance tasks based on operational feedback but lacks a formal international standard. -
Absolutely. MCP offers comprehensive support across the entire reliability journey—from assessment and strategy development to hands-on implementation, coaching, and staff training. We also provide guidance on integrating new technologies for condition monitoring and predictive maintenance, helping you embed continuous improvement into your operations.